If your Maintenance function is already doing the right work, and you are doing the work right, there are primarily three areas in which continuous improvement can further improve Maintenance Productivity. These are:
- Eliminating the wastes which prevent Maintenance work from being performed efficiently,
- Continuously improving the Preventive and Predictive Maintenance program, and
- Eliminating the defects which cause the need for Maintenance work
This is the fourth in a series of articles on improving Maintenance Productivity through the use of Lean Maintenance techniques.
Improving maintenance efficiency
In the previous article in this series – Doing the Work Right, we discussed the importance of detailed planning and preparation in advance of actually performing Maintenance work. However, despite our best intentions in this step, there will be times when we do not (or cannot) perform the work in accordance with the provided plan, or within the estimated time allowed for performance of the task. It is vitally important that we capture this information – or more importantly, the reasons why the work could not be performed as planned so that this can be investigated and, where possible, the underlying causes eliminated. In effect, we are trying to capture any delays that tradespeople encounter in performing their work, and the reasons for these delays occurring.
In the context of the work management framework introduced in Doing the Work Right we are introducing an extra step between Completing Work and Planning Work, as illustrated below.
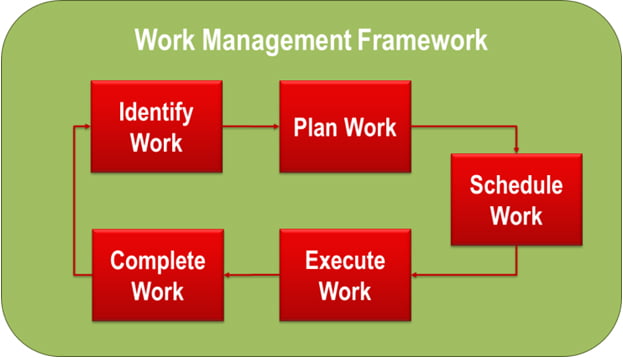
So how does this work in practice? We would encourage the tradespeople who are performing the work to note any delays encountered, their size and cause on the work order. Work order formats should permit the recording of this information. When the work order is closed out, these delays should be entered into an appropriate system (at least some CMMS/ERP systems can capture this information). On a periodic basis, aligned with the frequency with which Maintenance Schedules are issued (normally weekly or less frequently fortnightly), the delays and their causes should be summarised and reviewed at a Schedule Review meeting attended by both Operations/Production and Maintenance personnel. The causes should be discussed and the resulting actions to eliminate or reduce future similar delays should be noted and assigned to responsible people for completion. This can frequently be done as part of the routine Maintenance Planning cycle.
A prerequisite for this to work effectively is that tradespeople do actually record delays they encounter and their reasons on work orders as they perform the work. This requires their active involvement and cooperation. We will discuss this in more detail in the next article in this series “Environment for Success”.
It should be noted here that another possible approach for capturing and recording the delays encountered by tradespeople is through the use of Activity (or Work) Sampling. This involves periodically (at randomly determined intervals) observing what tradespeople are doing, and recording whether they are engaged in “Hands On Tool Time” or something else. If they are not actively working on the job, then what they are doing is also categorised and recorded. While this is a valid approach, it has a number of weaknesses.
- First, it is quite time-consuming for the analyst performing the observations, and so, at best, tends to be used as a snapshot of “Hands-On Tool Time” at a particular point in time (generally over a week or a month). This may or may not be representative of the longer term situation.
- Second, and more importantly, it has connotations of “Big Brother” watching over people, with all of the negative emotions that this generates amongst the people whose work is being observed. So much so that people will often modify their behaviours while the study is being performed, rendering the results inaccurate and of limited value. We recommend a more cooperative approach with the workforce as being better in the long run.
Improving the preventive maintenance program
In the second article in this series – Doing the Right Work, we discussed some key principles involved in ensuring that the Preventive Maintenance program was efficiently directed towards predicting and preventing the consequences of equipment failure. However, in developing an optimum Preventive Maintenance program we are frequently shooting at a moving target. Over time, several things change, all of which can have an impact on our decisions regarding the optimum Preventive Maintenance program. These include:
- Changes in desired Production rates, which in turn can impact on equipment deterioration rates
- Changes in the financial impact of failures and equipment downtime, often due to changes in external market conditions
- Modifications to equipment
- Modifications to operating/process parameters
- Ageing/deteriorating equipment (or replacement/refurbishment of equipment)
- A growing understanding of how (and how often) equipment fails, and the consequences of those failures
- Introduction of new technologies for predicting or preventing failures
All of these changes require us to review and improve the Preventive Maintenance program on a regular basis. Doing so will ensure not only that desired equipment reliability levels are maintained, but will also ensure that Maintenance labour is performing the required Preventive Maintenance, and not spending time on unnecessary Preventive Maintenance.
In practice, there should be three triggers for review of the Preventive Maintenance program on any equipment item or system:
- A change in equipment operating context, failure consequence or configuration (generally triggered as part of a Configuration Management/Management of Technical Change process)
- An unexpected equipment failure (we will discuss this further in the next section of this paper)
- Failing either of the above, a periodic review at some predetermined frequency (generally either annually or biennially)
Eliminating defects
The most effective and sustainable way of improving Maintenance productivity is by eliminating the need for maintenance altogether. This is generally achieved through a Defect Elimination Process.
Defects are those failings in our processes and systems which generate unwanted equipment failure events. They can be manifested in:
- Deficiencies in our Preventive Maintenance program
- Deficiencies in Maintenance repair/overhaul procedures
- Deficiencies in the way equipment is operated
- Deficiencies in equipment design
- Deficiencies in equipment manufacture
- Deficiencies in the way equipment is installed and commissioned
- Deficiencies in the specifications of spare parts purchased
- Deficiencies in the way that spare parts are stored and preserved
- Deficiencies in skills and competencies
An effective defect elimination process will actively and systematically seek out and progressively eliminate these deficiencies. It does this by identifying and implementing practical solutions to tackle the underlying root causes or unwanted events in a proactive and structured manner. Defect Elimination can be used both to address past unwanted future events (either one-off, significant failures or smaller, chronic repetitive failures) and to address potential future (but not, as yet, experienced) failures.
The following diagram shows a simplified view of a suitable continuous improvement/defect elimination process. This should be supported by an appropriate set of formal root cause analysis tools, such as “5 whys”, cause and effect trees and fishbone diagrams and adequate training for personnel in the use of these tools.
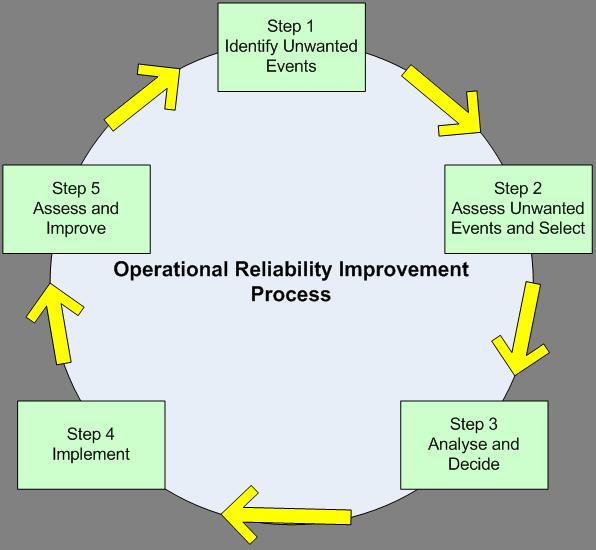
One of the key things that High Reliability Organisations have learned is that far greater and more sustainable business benefits are achieved when focusing on eliminating the causes of failures, rather than just predicting or preventing them. Most organisations, in their attempts to improve maintenance productivity focus on improving Maintenance Planning and Scheduling processes. However, their attempts are frequently thwarted as unexpected failures disrupt their ability to successfully complete all planned work that has been scheduled. Successful organisations have increased the amount of planned work that they performed, not by focusing on maintenance planning and scheduling, but by instead focusing on defect elimination – eliminating the causes of unplanned work.
Conclusion
In this article, we have discussed three ways in which continuous improvement approaches can further improve Maintenance Productivity and eliminate waste. However, embedding this continuous improvement culture within an organisation is not easy. We will discuss this further in the next article in this series “Environment for Success”.
Do you need a more effective preventive maintenance program?
We have over 21 years of experience in improving maintenance programs for a wide range of industries. Our services are catered to your specific business and operational goals, and we aim to be proactive in delivering solutions that are grounded in practicality and bottom-line results. Sound good to you?