In this article, we will tackle the second of the 5 keys to Lean Maintenance and Maintenance Productivity Improvement – doing the work right.
“Insanity: doing the same thing over and over again and expecting different results.”
Albert Einstein
This is the third in a series of articles on improving Maintenance Productivity through the use of Lean Maintenance techniques.
In the first of this series of articles, 5 keys to Lean Maintenance and Maintenance Productivity, we discussed the benefits that leading organisations enjoy when they have high levels of maintenance productivity, and outlined five ways in which maintenance productivity may be improved. These were:
- Doing the right work
- Doing the work right
- Focusing on continuous improvement
- Creating an environment for success
- Thinking holistically
As we stated in 5 keys to Lean Maintenance and Maintenance Productivity, once we’ve determined the right work that needs to be done, to get the best from the limited resources we have, the work needs to be executed efficiently and effectively. Sounds logical, however, the best developed, waste minimised maintenance program in the world is of no value in reducing/eliminating waste if the program is not properly implemented and executed. Ensuring the proper implementation of your maintenance program is a subject we’ll cover in a future separate article.
Executing the right work: a work management framework
In the second article in this series, 5 keys to Lean Maintenance and Maintenance Productivity – Doing the Right Work, we talked about determining the right work that needs to be performed by removing waste from your preventive maintenance program. So now that we’ve determined what this work should be (removing any unwanted waste perhaps through an RCM based process) let’s assume that your program has been properly set up and the ‘go’ button has been pressed. We need to have an effective maintenance work management framework in place to ensure the right work is being done right. This framework consists of the processes shown in the diagram below.
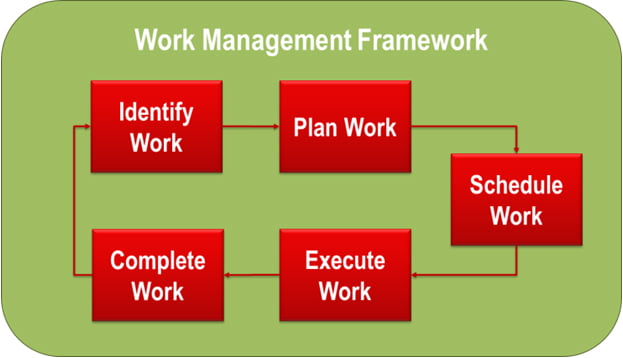
Without these processes in place, maintenance staff waste time and effort on discovering what they should be doing, prioritising tasks, identifying required resources (tools, parts, people), working out when work can be done, waiting, travelling etc; all time that could be used for conducting ‘real’ maintenance activities!
Our intention with this article is not to describe what does good maintenance planning and scheduling look like, but rather to focus on key elements within each of the Work Management Framework processes that will produce improvements in maintenance productivity and remove waste. Let’s now look at each of the process steps in turn, highlighting these key points.
Step 1: Identifying the work
Identifying the work has two main stages:
- Initial identification and filtering of potential work
- Prioritisation of real work.
Initial identification and filtering of potential work
In addition to Preventive Maintenance work orders (the right work) which will be generated automatically by our CMMS at required intervals, maintenance personnel will also be required undertake work of a corrective nature on equipment that has failed or is about to fail. This corrective work is identified as either Breakdown Maintenance, ie. fix it ASAP, or Scheduled Corrective Maintenance, ie. plan and schedule the repair.
For this corrective work, a key focus is to ensure the individual concerned is able to actually articulate clearly the description of the fault/issue that needs to be dealt with. Descriptions in vague and general terms don’t help supervisors and planners identify the problem and results in additional time being wasted trying to uncover the actual problem, and hence the corrective action required. Ideally in raising a Work Notification/Request, there should be clear and concise description of the equipment, its location, and the problem encountered. The author should avoid attempting to provide a fix to the problem in the description as any suggested fixes may only address the symptoms and detract from focussing on the real problem.
Clearly articulated Work Notifications/Requests will also assist with filtering to ensure that only the ‘real’ work is actually acknowledged and progressed into a Work Order. Descriptions in vague and general terms can also lead to time being wasted in the filtering process as a result of trying to uncover a problem that isn’t ‘real’ work.
Ideally the identification and filtering for all new Work Notifications/Requests needs to be performed at least daily. This minimises the risks associated with failure by then allowing the appropriate prioritisation to then be applied to the Work Order and subsequent execution undertaken.
Prioritisation of real work
With the ‘real’ work now identified as legitimate Work Orders, there needs to be a clear process for the prioritisation of these Work Orders to ensure that those that represent the greatest risk to the business receive the highest priority for subsequent planning, scheduling and execution. Prioritisation of Work Orders cannot rest solely on the planner. The process needs to involve consultation with representatives from both the operations and maintenance areas who are able to provide input as to the business risk associated with each Work Order and then provide relative ranking in comparison to other existing or newly created Work Orders. Ideally this prioritisation for all new Work Orders should be performed at least daily. This will minimise the risks associated with failure by allowing the appropriate prioritised planning and scheduling to be then undertaken.
Step 2: Planning the work
With a prioritised list of Work Orders, appropriate planning of the work can now be undertaken. Some key areas of focus in planning for minimising waste are:
Clear identification of all resources, internal and/or external, required to perform the work. This includes labour, parts, tools, any special equipment, and the order/sequencing of the tasks required, eg. erect scaffolding (external resource) before tank cleaning (internal resource). There should also be some preliminary determination of the availability of these resources to assist with scheduling of the work.
There should be a thought out and documented method/procedure to the work, especially if the work is complex and/or could reasonably be expected to reoccur at some time, eg. replacement of a valve. If the work hasn’t been documented or occurred previously, it would be worth the planner to visit and inspect the site to ensure nothing is missed, eg. in order to get to A you need to remove B with a crane.
Work instructions need to clearly articulate the key activities/checks required in order to ensure the work is performed to an appropriate standard and thereby avoid potential rework. The ability to make any changes to the instructions may not be able to be performed during the planning step, however, identification and forwarding to the appropriate maintenance/reliability engineer for action as part of the process of Continuous Improvement.
Step 3: Scheduling the work
With Work Packs at the ready, the work can now be scheduled. Some key areas of focus in scheduling for minimising waste are:
Before scheduling the work, ensure that all the resources, both internal and external, will now be actually available for when the work is intended to be scheduled.
Say the schedule of work for the next week has been developed, agreed between operations and maintenance, and is now locked in. The work of the planner is not, however, complete. At some time shortly before the actual scheduled execution of the work, the planner needs to ensure that all the resources required to perform the work will actually be present before the work commences. For example, making sure the day before that all required parts are available, preferably picked and gathered in one location, and any large items pre-positioned to the job site. The will ensure maintenance personnel spend their time productively on the actual work and not waste it searching for parts, waiting for contractors, raising permits etc.
On the day the work is to be executed, the workload will need to be balanced and adjusted with the actual available workforce on the day. Balancing this workload will require agreement between operations and maintenance on what will and will not be performed in order to ensure the workforce is fully productive and time is not wasted performing now unnecessary tasks. For example, operations would waste time shutting down and cleaning equipment if there were insufficient maintenance personnel to undertake the work.
Step 4: Executing the work
‘To err is human’ and ‘nobody’s perfect’. As humans, regardless of whatever field, we all make errors. However, through design of systems, both physical and procedural, what we try to do is make it hard for personnel to do the wrong thing and easy for them to do the right thing. When it comes to executing the work, some key areas of focus in minimising waste are:
Supervisors need to make clear to their workforce the expectations around the work duration and quality. This should ideally be performed each time a job is allocated to ensure there are no misinterpretations of the expected outcomes.
Work should be allocated by supervisors to their workforce one job at a time. The allocations should be based around priorities and resources. Trades personnel should not be permitted to select their own jobs from a list available for the day otherwise natural human tendency will be to choose the path of least resistance. This means easy jobs would be completed first but they may not be of the highest priority. This becomes an important factor in mitigating the risks and potential waste when Breakdown Maintenance work is required to be performed by the same workforce.
Once allocated and underway, supervisors need to regularly follow up on the allocated jobs to ensure their workforce is meeting the expectations of duration/schedule and quality for the work. This will ensure prompt action is taken for any identified issues. As per the title, supervisors need to supervise. Supervisors cannot supervisor from behind a desk in an office.
There needs to be a formal process involving operations and maintenance for the authorisation, prioritisation and allocation of all Breakdown and Break-in Maintenance work. This will ensure the effective and efficient use of available resources and the minimisation of any resultant risk (from scheduled work not being able to be completed or operations not getting the equipment back at the originally scheduled time).
Step 5: Completing the work
The final step is making sure that when the work is complete, the Work Order records all the relevant information that is necessary to support your organisations’ needs and objectives. Some key areas of focus to minimise waste in completing the work are:
Ensure the trades personnel a clear on the content and quality of the information that is required to be captured in the completed Work Order as the information will be used to support the Continuous Improvement process (in addition to administrative recording/reporting processes). Garbage in, garbage out…which then becomes a waste of everyone’s time. Trades personnel should also be encouraged to comment and offer suggested improvements on any areas of ambiguity or confusion in Work Instructions. This feedback is important to ensuring improvement of the instructions to remove any potential waste. Our next article, 5 keys of Lean Maintenance and Improving Productivity – Continuous Improvement will discuss this in more detail.
Consider who is best to close out the Work Order. A trades person, who is a better source for ensuring the quality of the information recorded, or a clerical assistant, who provides more time for the trades person to focus on completion of work.
Work management monitoring
Monitoring the performance of the whole Work Management Framework will assist with the identification of any waste that can be minimised through the process of Continuous Improvement. In our next article, 5 keys of Lean Maintenance and Improving Productivity – Continuous Improvement, we will discuss the how monitoring and measuring the Work Management Framework can assist with minimising waste and improving productivity.
So far in in determining the right work and then doing it, we’ve looked at ways of minimising waste to improve productivity. Further tools are needed to identify and eliminate causes of issues such as equipment failures, service overruns, lack of required resources and poor schedule adherence which result in waste.
In the next article in this series, we will discuss how to put in place effective Continuous Improvement processes in place to reduce or eliminate waste and improve productivity.
Do you need a more effective preventive maintenance program?
We have over 21 years of experience in improving maintenance programs for a wide range of industries. Our services are catered to your specific business and operational goals, and we aim to be proactive in delivering solutions that are grounded in practicality and bottom-line results. Sound good to you?