An Australian iron ore company who control the rights to a large tenement portfolio across the Pilbara region was conducting a mine and market pre-feasibility study of the one of their Iron Ore Projects.
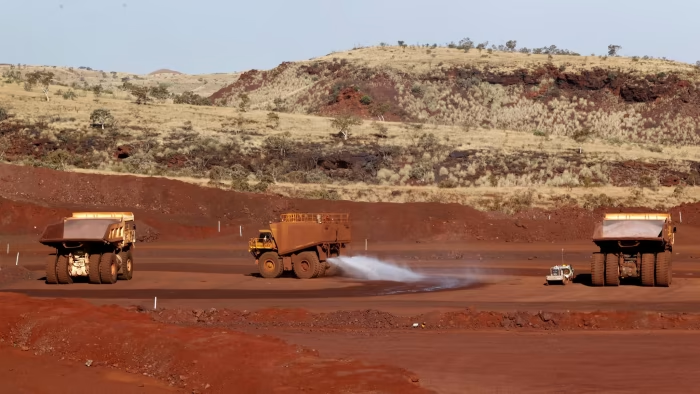
The Australian iron ore project problem
To support this pre-feasibility study, the client required assistance to estimate the maintenance and operating cost for the operation of the central processing facility and power generation plant.
Our solution for maintenance and operating costs
We developed a bottom-up model to estimate the cost. This provided the client with a model that could be further enhanced and developed as the project progressed through Bankable Feasibility and Detailed Design. The model provided the following information:
- Maintenance and operations manning requirements for “business as usual” and major outages
- A preliminary organisation structure design for operations and maintenance
- Operating costs for the processing facility and power generation plant
- Consolidation of the total maintenance costs including labour, material and equipment
- A cost estimate for the initial procurement and ongoing consumption of critical spare parts
Our approach
Our approach included the following steps:
- Build detailed models. Drawing on both the client’s experience and our own, a set of best practice maintenance strategies were allocated to each equipment type. Consolidation of the maintenance strategies provided the basis for developing a draft shutdown calendar which in turn was used to model the feasibility of different shutdown strategies. This was then refined to estimate the overall maintenance and operation cost for the processing facility.
- Model customisation. The models were adjusted for the specifics of the client’s operating context and expected equipment performance. At this stage an organisation structure was developed in order to identify the supervisory and managerial levels required.
- Analyse output and verify model. The model output was analysed and with the assistance of the client adjusted to reflect a realistic result.
- Reporting. A report was prepared, which recorded the major findings and captured all methods and assumptions. The Results A detailed cost model was delivered to the client that included the following:
- Best Practice Maintenance strategies for all equipment
- A draft shutdown calendar
- An organisation chart and personnel cost
- Cost profile across the life of the mine.
- Breakdown of the $ per tonne contribution of:
- Manning Cost for both internal and external labour
- Material cost
- Operating cost
- Energy cost
- Cost for support vehicles and equipment
The report contained all the major findings and assumptions contained in the model.
The detailed bottom-up approach permitted maintenance and operating costs to be estimated with a high level of confidence. In addition, the approach taken and the model provided allows a high level of flexibility as the preliminary design of the project progresses, and equipment details or operating context change.
Ready to get the best value from your assets?
We offer a comprehensive range of consulting services relating to maintenance, reliability and asset management. If your needs are comparatively straight forward, we have standardised approaches for delivering these services that provide demonstrated results as quickly and cost-effectively as possible. Browse our services below to explore how we can help to achieve your goals.