Automation is being adopted by many organisations that may be new to the concept of Configuration Management. How do they address this challenge?
With the introduction of automation not only in our daily lives but also in asset-intensive industries, the processes to maintain and manage the configuration of these assets has become more complex. This article ‘Challenges of Configuration Management in the Age of Automation’ aims to look at some of the challenges that can be experienced in managing the configuration of automated assets and how these challenges can be addressed.
Automation
Automation is making headlines especially in mining since many drivers on dump trucks, mining drill rigs and heavy haul trains have been asked to move over in favour of ‘the machines’. But automation has been around for quite a long time. Earliest automated functions used the centrifugal governor to govern the gap between millstones. This concept was used for the development of the steam train as well. Autopilot has been around for many years. According to Wikipedia the first aircraft autopilot was developed by Sperry Corporation in 1912. “The autopilot connected a gyroscopic heading indicator and attitude indicator to hydraulically operated elevators and rudder. It permitted the aircraft to fly straight and level on a compass course without a pilot’s attention, which greatly reduced the pilot’s workload”[1].
Recently this type of technology is applied in a wider range of industries, one example is iron ore mining. The big iron ore mining companies embarked on the journey towards automation as a means to reduce cost, improve productivity and improve safety. Notably mining haul trucks and heavy haul rail. They are also automating the drilling and loading processes. Drill rigs have been automated, and development work is underway to automate loading by large scale shovels as well.
Looking after complex systems
Everyone is potentially aware of driverless cars, and these are being tested by Google. Automation is certainly a buzz at the moment but what are the implications of it all. We will look at why automation has brought configuration management to the fore, as an essential discipline in supporting increasingly complex systems.
We are relying on automated processes to make decisions that could have a higher level of impact. It is not hard to imagine that driverless cars, trucks or trains could cause loss of life or multiple lives in case something goes wrong.
The relevance to configuration management here is that the impact of decisions made by machines is carrying a higher level of risk and could affect lives, not only the lives of employees but also the public.
Automation still requires humans
Quoting Elaine Schwartz on econlife.com “And therein lies the paradox. The less humans need to know because of automation, the more they should know.”[2] Automation is getting more complex, and the human involvement is becoming more important – not only to develop and set it up but also to maintain, operate and improve it.
Automation inevitably requires software, hardware, data or settings and also physical inputs to operate. These inputs are all dependent on the human factor for installing, uploading, constructing or setting up. For example, an autonomous train as found in public transport or potentially mining, may be dependent on the wheel diameter of the locomotive to measure the distance travelled, and therefore the train has an accurate understanding of where it is located on the rail network. Wheel diameters are programmed into the automation system software or data by technicians. If for instance the on board ‘automation computer data storage device’ need to be replaced, how do we make sure the correct wheel diameter is loaded onto the replacement data storage? If the wrong configuration data is loaded it may result in the train not slowing down in time for a turn or not stopping in time for some reason. Since us as humans are prone to forget or make mistakes, it is important to have processes and systems in place to make sure the correct configuration is used. The same would apply for installing incompatible software or firmware or physically installing a limit switch or marker in an incorrect location.
Configuration management
It is therefore clear that without configuration management we could expose ourselves to serious consequences. What does Configuration Management Offer? Configuration management is part of the Change Management process. According to An Anatomy of Asset Management by The IAM[3], Configuration Management identifies, records and manages the functional and physical attributes of assets, software and related documentation including the links between the components of a system. For example, Configuration Management ensures that only compatible software version are installed on a system. The image below shows how compatibility (and Configuration) could be controlled.
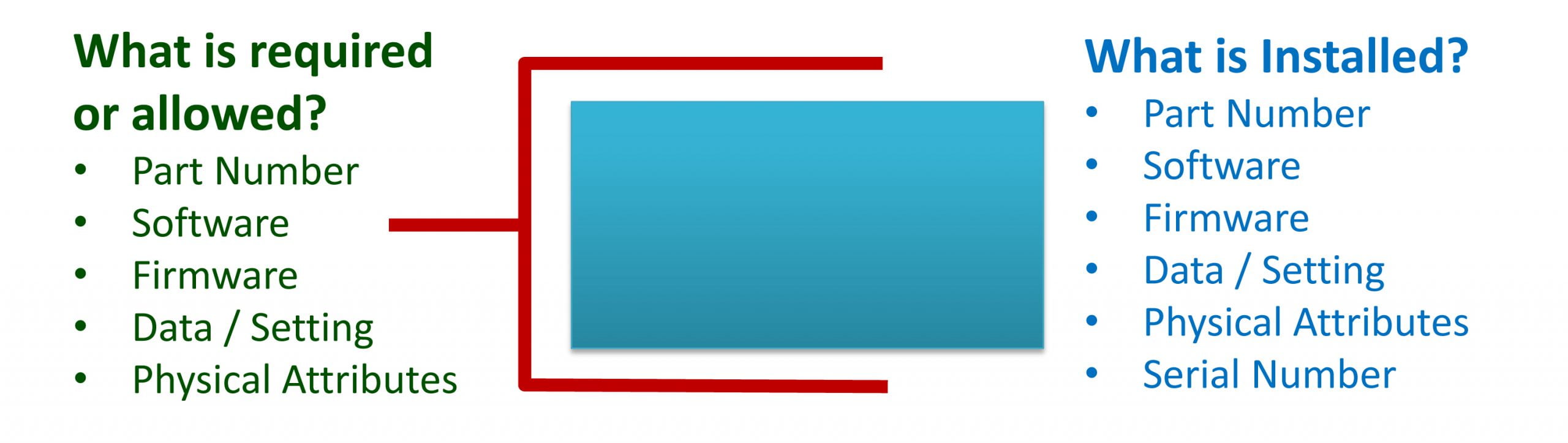
Same would apply to mechanical systems where only compatible components would be allowed to be installed. This implies that there would be a baseline definition of what is allowed, what is compatible and therefore what can be installed and what cannot be installed (or uploaded).
According to ISO 10007, Configuration Management consists of 5 elements namely Management and Planning, Configuration Identification, Configuration Control, Configuration status accounting and Configuration verification and audit[4].
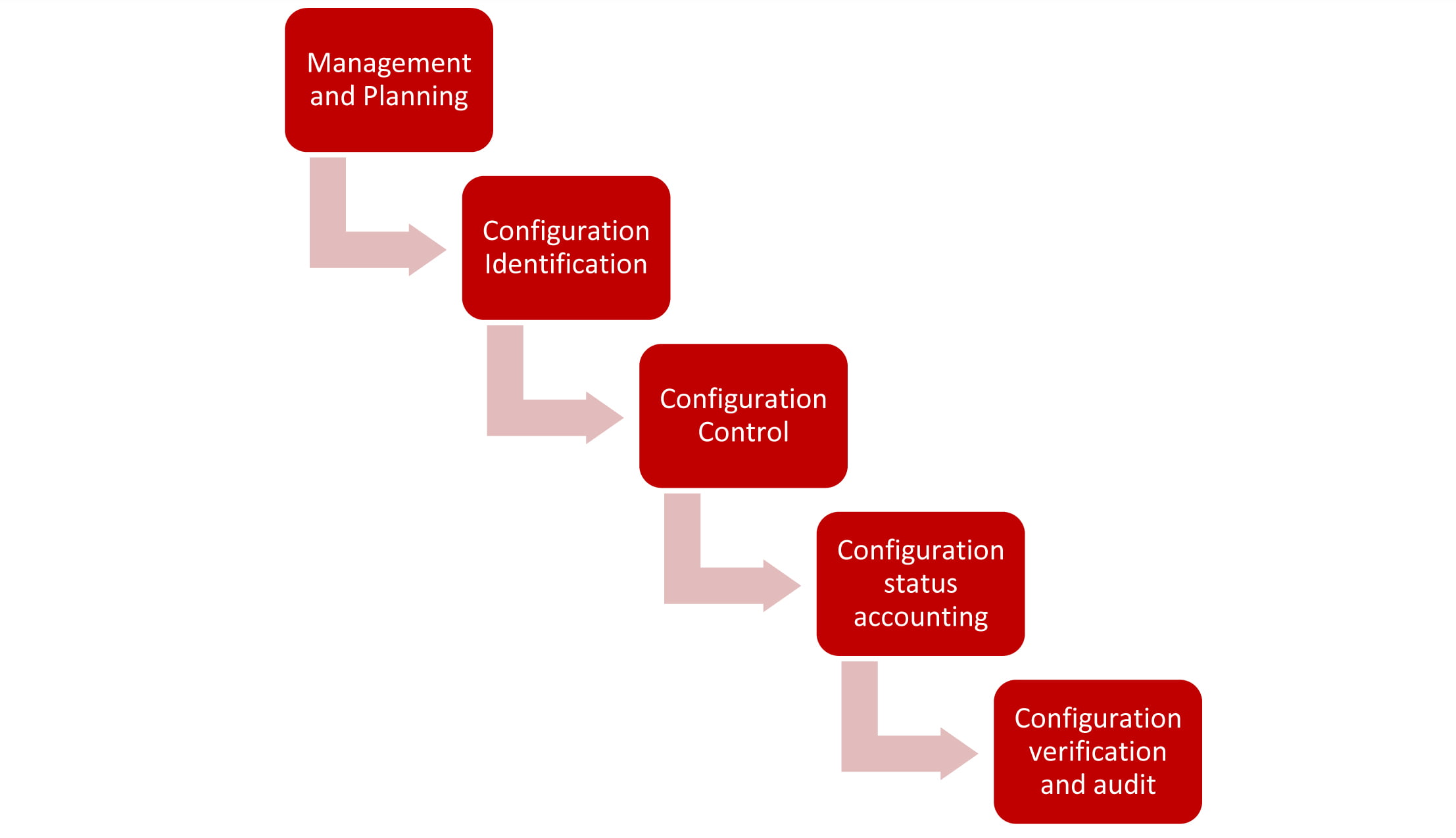
Management and planning cover the leadership aspects of setting the direction, documenting the minimum requirements and expectations and the basic processes required for good configuration management.
Configuration Identification requires the identification of candidate items that need to be configuration managed. This is usually based on an assessment of the risk of failure or the risk incorrect configuration would have on the business.
Configuration Control refers to the process of managing the configuration on an asset through its life and how to deal with changes.
Configuration status accounting includes the capturing and management of all configuration data.
Configuration verification and audit require processes to be put in place to verify that the physical configuration corresponds to the configuration data as represented by the configuration management system data.
Challenges in the operate and maintain stages
Configuration Management is relevant to all the life cycle stages of an asset. A high degree of Configuration Management is required during the acquire stage for proper systems engineering to take place, but the focus here is on the operate and maintain stage as this is where, especially for automated equipment, configuration management doesn’t get the focus it deserves. This could be because the equipment is now being operated and maintained by a user that potentially don’t have the same level of technical understanding as the design engineers that were involved during the acquire stage. What are the challenges for the operator or maintainer of the equipment related to configuration management in a highly complex system, where the outcome of a failure could have catastrophic consequences?
The following points describe a few examples of the challenges in configuration management in the operate and maintain phase.
- How does an operator know that the equipment is safe to use? After the equipment has been repaired or serviced, the operator may receive the go-ahead from the maintainer or service supervisor but how can the operator verify that the configuration of the equipment is correct? e.g. the correct wheel diameter is loaded, or the correct version of Google maps have been loaded in the example of a driverless car.
- Who signs off that the equipment configuration is correct after maintenance? Is it the maintenance supervisor that signs off after maintenance has been completed to confirm that the equipment configuration is correct and safe?
- How does the maintainer know which is the correct part? Does the maintainer have to rely on a scratched or faded equipment label to read the hardware version or part number? Does he or she understand the difference between Part Number QX9AAA123 and QX9AAA123-01? Is the maintainer provided with the correct data to ensure the correct part is used?
- How does the maintainer know the software version was correctly loaded? Is there a possibility that the software could be loaded successfully but may not work under operational conditions?
- What history does the maintainer need to record? Does the maintainer need to record the serial number of each and every component that was replaced?
- How does the storeman bin compatible and incompatible parts? If the vendor delivers a part to the store will the storeman be able to verify that the correct part has been delivered? Does the storeman bin QX9AAA123 with QX9AAA123 -01 and if a work order requests a QX9AAA123 part number can he supply the QX9AAA123 -01 part if that is all he has?
Addressing the challenges
How do you set up configuration management to address the mentioned challenges?
The starting point would be to develop all the elements as described by the ISO10007 standard. That includes the steps described below.
Write a configuration management plan that lays the ground rules for how you want to manage the configuration of your assets.
Identify the CM candidate items carefully. You may decide to have different levels of configuration management depending on the level of criticality of the asset. Configuration management is an expensive process and need not be applied to all equipment or all maintainable items.
Awareness is key to making the process work. Configuration Management affects many parts of the organisation and therefore a lack of awareness in operations or supply could have serious implications. Creating awareness through training and communication will be essential to successful configuration management.
Consider what measures need to be in place in order to make sure the configuration management process is executed as intended. The best mechanism to have in place is a culture of understanding of the consequences and disciplined configuration management. Measures could be put in place to do quality assurance on the Configuration Management System (CMS) or your Computerised Maintenance Management System (CMMS) transactions that were completed. The supervisor could also be tasked to perform a certain number of spot checks per week and compliance of that requirement could be measured.
Auditing the Configuration Management System and Processes will provide the user with an independent view on how well configuration is managed. Audits need to occur at regular intervals and it is recommended that external audits be used to ensure independence.
Configuration management is built on and dependant on sound engineering, maintenance, operations and supply procedures. If these are not robust or are not being followed it becomes increasingly difficult to manage the configuration of your assets. Therefore ensure that the overall Change Management Process, Work Management and Supply Management processes in the organisation are being followed.
Manufacturers are in many cases brought in to maintain and manage the configuration of the equipment. There are benefits to this but an awareness of the implications are still required by all role-players. Setting up outsourcing agreements and ensuring clear delineation of responsibilities are imperative in this situation.
Configuration Management requires a high level of awareness of the consequences and a high degree of discipline which in short means having a culture that understands and supports configuration management.
Evolution of configuration management
Another mechanism for addressing the challenges of configuration management is to make use of the automation technology that put us in this position in the first place. Configuration management started on paper-based systems that for example captured what weapons was fitted to certain aircraft to execute certain missions.

Configuration management has been managed using databases for many years and the application of this technology is widespread. The next evolution, which is also in widespread use is ‘system managed configuration’, where the system does its own internal checks to verify that the configuration of the asset is correct before it is operated. This is the preference and should be made part of the systems requirements when developing automation systems. There will always remain a physical element that could potentially not be controlled by systems managed configuration management but checks and balances should (and are) being built into the system to eliminate the consequences of human error.
Conclusion
In summary, automation is a bandwagon that will be jumped on by many organisations that may or may not have experience in managing the configuration of complex systems. Until such time as the machines will look after themselves, we will need leadership that inspires a disciplined culture in order to ensure we are not being exposed to high levels of risk.
[1] Wikipedia, “Autopilot,” Wikipedia, para. 4, Feb. 16, 2016. [Online]. Available: https://en.wikipedia.org/wiki/Autopilot. [Accessed: Feb. 19, 2016].
[2] E. Schwartz, “The Paradox That Automation Creates,” econlife.com, para. 6, Jul. 6, 2015. [Online]. Available: http://www.econlife.com/the-paradox-that-automation-creates-for-human-capital/. [Accessed: Feb. 19, 2016].
[3] The Institute of Asset Management, An anatomy of Asset Management, 3rd ed. Bristol, The Institute of Asset Management, 2015.
[4] Standards Australia International, “AS ISO 10007-2003 Quality Management systems – Guidelines for Configuration Management,” Sydney, 2003.