An organisation’s asset register is the foundation on which its Asset Information systems are built. Dodgy foundations mean a rickety building. Here are 5 tips to make sure your Asset Register is rock solid.
1. Understand why you need an asset register, and what you are going to use it for.
We often take an asset register for granted – most organisations already have one – but unless you clearly understand what you are going to use it for, then there is a risk that the asset register you develop won’t meet your needs. An asset register is important to many people in your organisation, and is used for many purposes:
- Accountants and auditors need an asset register so that the organisation’s balance sheet can be accurately calculated, and that the organisation’s accounts meet the needs and mandatory requirements of investors and external regulatory authorities (such as the Tax Office)
- Accountants also need the asset register so that they can apply the appropriate depreciation amounts to assets owned
- Accountants may also need to use the asset register so that they can make appropriate insurance or warranty claims in the event of loss or damage to the equipment
- External regulators may require the asset register so that they can identify any equipment requiring mandatory maintenance, and also verify that the required maintenance has been performed on this equipment
- Maintenance personnel need the asset register so that they can effectively plan and schedule maintenance activities required on equipment, and record maintenance activities that have been completed
- Reliability and Maintenance engineers need the asset register so that they can identify assets that are underperforming, and that may need reliability improvement activities performed on them – or may need replacement.
- Operations and Maintenance personnel need the asset register so that they can easily identify equipment by name or number, and communicate maintenance or operational needs associated with the equipment effectively and efficiently
You can see that there are many different stakeholders who require different things from the Asset Register. It is important, therefore, to consider their differing needs when developing your Asset Register. The benefits of an accurate and useful Asset Register include:
- Assured compliance – with the requirements of financial, safety, environmental and other regulators
- Preventing fraud – an effective asset register allows you to more easily identify assets that have been lost or stolen.
- Cost reduction – a sound asset register assists with the identification and implementation of actions to improve operational performance
2. Establish a logical hierarchy of assets
One of the keys to making the asset register easy to use for operational and maintenance personnel is to establish a formal hierarchy of assets. This has several benefits including:
- Being able to “drill down” through a hierarchy to find an asset in the register when you are unsure of the asset name or number
- Being able to group together assets that belong to a related system – which makes it easier to determine the asset value for the entire system, to archive the system (when it is sold or scrapped), or to determine related equipment when planning maintenance shutdowns
The most common way of structuring the hierarchy is to start at the top and work down. ISO 14224 (the international standard for collection and exchange of reliability and maintenance data for equipment) offers a framework for the hierarchy as shown in Figure 1 below. The standard offers definitions for each of the levels in this hierarchy, and also gives examples (from the oil & gas industry) to illustrate the definitions.
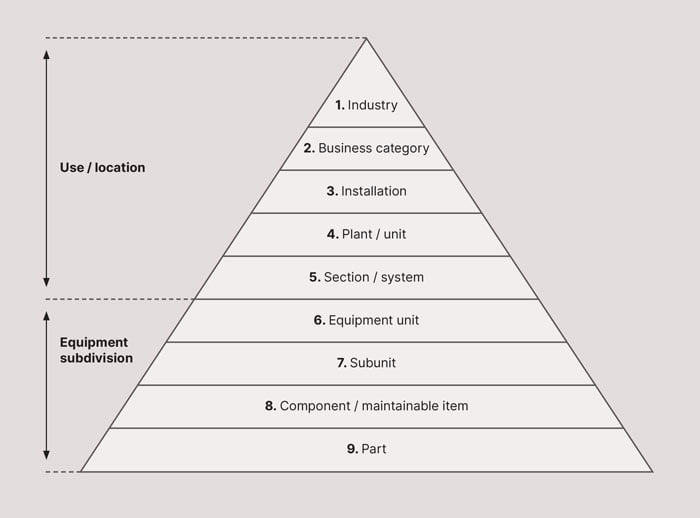
Some of the subtleties involved in setting up the hierarchy are perhaps not evident in Figure 1, or explicitly discussed in ISO 14224. For example, if you consider a pump set (which, for example, consists of a pump and electric motor), should you consider the pump set as one being at one level in the hierarchy, with the motor and pump as “children” to the pump set in the hierarchy? What about the suction and discharge valves for the pump – where in the hierarchy would they sit? Are they children of the pump, or should they be associated with the pipework? There is no single correct answer to these questions – but the important thing is that you have considered these, and that whatever decision you arrive at should be consistently applied across all equipment. Otherwise this will cause confusion amongst your maintainers and operators.
3. Establish structured, easy to understand numbering and naming conventions
Another key consideration is how to name and number your assets. Names and numbers should be easy to understand so that equipment can easily be identified and names and numbers easily remembered. While it will be possible to identify equipment within your Computerised Maintenance Management System (CMMS) or Enterprise Resource Planning (ERP) system without a logical naming system if you have set up the hierarchy properly in line with Tip 2 above, it will be much easier all round if you can remember the name and/or number of equipment without having to drill down through a hierarchy.
Most CMMS/ERP systems will automatically add an equipment number as a unique identifier when you add equipment to the register, but this will almost certainly just be a number allocated in sequential order, and not easy to understand. It will be far better to set up a structured numbering system – which potentially aligns with the hierarchy that you have set up. A possible numbering system might look something like the following:
AAA-BBB-CCC-000-DDD
- AAA is a three-character alphanumeric code identifying the equipment unit (e.g. OP1 = “Ore Processing Unit 1”)
- BBB is a three-character alphanumeric code identifying the subunit (e.g. CR1 = “Crusher 1”)
- CCC is a three-character alphanumeric code identifying the maintainable item (e.g. LUB = “Lubrication System”)
- DDD is an optional three-character alphanumeric code identifying the component (e.g. PT1 = “Pressure Transmitter”)
Obviously, this is just a suggestion, and the number of levels in the equipment numbering structure, and the number of characters at each level may (and probably should) vary to suit the specific needs of each site. However, the numbering system and the codes used should be consistent across each site. Consistency is vital. It also helps to be consistent when there are several identical equipment items in a bank (for example in a bank of pumps). Try to make sure that the numbers increase in value when you go from North to South (or East to West), for example, for all banks of equipment.
Naming conventions should be equally consistent. For example, is there any difference between a “tank”, a “vessel”, or a “vat”? If there is, then make sure everyone is aware of when to use which term. If not, then it will be much simpler to standardise on one name only.
Consistency is also vital when considering alignment with other documents and drawings that may exist for the equipment. For example, if your Process and Instrumentation Diagrams (P&IDs) contain equipment numbers and names, then these should ideally be the same as is used in your CMMS/ERP system in order to avoid possible confusion. It makes sense, therefore, for new plant and equipment, to agree on the naming and numbering convention with your project engineering team before they start designing the plant.
4. Understand and define the differences between locations, equipment and components
CMMS and ERP systems often differentiate between locations, equipment and components – even though these can relate to assets at different levels in your equipment hierarchy.
To understand the difference between a location and equipment, consider the situation at a power station where you may have several identical boilers and several identical boiler feed pumps. The first boiler feed pump on Boiler 1 may be assigned an Asset code such as BLR1-BFP-001. However, the pump that occupies that location may be able to be removed (and replaced with a rotable spare), overhauled and returned to warehouse stock. When it is reissued from stock, it may be reinstalled in a different location (e.g. BLR2-BFP-001 on Boiler 2). In this situation, BLR1-BFP-001 and BLR1-BFP-001 are locations. If all you want to do is record information (such as costs and maintenance activities performed) against the location, then you can safely use the location code for doing that. If, however, you want to record this information also for each physical item (in this case, the pump) regardless of its installed location, then you would also need to establish a separate naming and numbering schema for the equipment, as well as location. Your CMMS/ERP would also need to be capable of managing this information, and allow you to install and uninstall specific equipment items in given locations.
So one of the key decisions that you need to make is whether you want to record activity and costs against both equipment and location – and if so, which equipment/locations you want to do this for. Clearly, it only makes sense to do this for equipment which can be moved from one location to another – and also for critical or high cost equipment where (for example) repair vs replace decisions may need to be made for specific equipment items.
Components and parts are lower in the hierarchy, and typically have less information recorded for them. Indeed, it is generally not possible to assign a maintenance work order to a component or part – but the definition of what constitutes a component or part is often discretionary.
There are benefits in limiting the number of assets that you classify as equipment:
- it makes the asset register more concise,
- the asset register is easier to navigate,
- it tends to be easier to find assets in the hierarchy,
- it is more likely to result in work order information being recorded against the right asset in the hierarchy, and
- maintaining and updating the asset register as plant configuration change is a much easier exercise.
However, if you do not establish all assets as individual items in your asset register, then it makes it more difficult to collate and analyse data for those assets. So you should give careful consideration to what level of detail you need, and establish clear rules for deciding whether an item is required to be recorded as an individual asset in the asset register. Things to consider in establishing these rules include:
- Depreciation rates – for accounting purposes, items with differing depreciation rates should be recorded separately in the asset register. Otherwise, depreciation calculations become more difficult than they need be
- Statutory requirements – is there a need to be able to easily track the performance of mandatory inspections or maintenance against the specific asset. If so, then you may find it easier for reporting purposes to include items subject to statutory maintenance as individual assets in the asset register
- Asset criticality – what is the impact of asset failure on your organisation? If the consequences of failure events of a specific asset are significant, and therefore these events need to be closely tracked, analysed and minimised, then it would be best to establish that asset as an individual item in your asset register
- Costs – is the item expensive to purchase or maintain? Effective management of costs will generally require that these assets are established separately in your asset register.
- Warranty – items for which you want to separately track warranty information (in order to be able to claim warranty in the event of premature failure) are most likely best established as separate items in your asset register.
As a general rule, however, try to minimise (within the constraints above) the number of assets you establish in the asset register. Doing this does make the asset register easier to manage, and also leads to better, more accurate information for analysis and decision-making. One of the traps that we have seen some organisations fall into is establishing every item that has an item tag on a P&ID in the asset register. This is most often an issue when dealing with instrumentation. There is often little value in separately itemising every element in a flow control loop in your asset register, for example. It is unlikely that you would ever analyse separately the costs or performance of the flow transmitter, flow controller and flow control valve – even though these may have separate tags in your P&ID. Better to just record the loop itself as the asset, with the individual items as components of that system.
5. Only collect and store asset information that you will use
Most CMMS and ERP systems have the capability to store lots of information regarding each asset. But populating every field takes time – time that is potentially wasted if you are not going to use the information recorded. For example, recording warranty information is of little value if you don’t have a system in place to ensure that all possible warranty claims are investigated and initiated if justified – or if the value of the item is so small that the cost of progressing a warranty claim exceeds the potential benefits.
Key information that you are likely to consider recording, however, includes:
- Asset ID: A unique identifier for the asset. This may be a sequential number allocated by your CMMS/ERP system
- Asset Number: As discussed earlier, using a structured numbering system is highly recommended
- Asset Name/Description: The description should be user friendly – what is it actually called by those within your organisation. This may be different to what the manufacturer or the supplier calls it. You may want to establish a separate field for the description of the asset according to the manufacturer/supplier if this is important to you.
- Serial number: If required, this would normally be a number provided by the manufacturer. If the asset is to be a rotable item (able to be moved from location to location), then you will generally need to populate this field. Otherwise it may be optional.
- Equipment Location: where the asset is installed. Most useful where assets may be moved from location to location
- Cost Centre: Required for effective cost management and control as well as for accounting reporting purposes.
- Date of purchase: This is generally important for accounting purposes.
- Purchase price: Also important for accounting purposes
- Warranty information: Only if you are going to track warranty for the item.
- Date asset placed in service: Also generally important to accountants for depreciation purposes.
- Depreciation details: the method for calculating depreciation and the key parameters for that calculation
- Equipment Class: this is often useful for grouping like assets together for analysis purposes – e.g. all vehicles may belong to a single equipment class
- Equipment Subclass: this may also be useful if you need to analyse a subclass of equipment. For example, you could establish a subclass for each specific make/model of vehicle. Some CMMS/ERP systems allow you to set up standard Preventive Maintenance programs and other documentation against a subclass of equipment, which assures consistency and makes system maintenance easier
- Statutory Equipment Flag: this allows you to identify any equipment which is subject to mandatory statutory maintenance or other regulatory oversight.
Conclusion
This article has offered five tips to make sure your asset register best meets the needs of your organisation. If you would like further guidance or assistance in establishing or improving the asset register in your organisation, please contact me. I would be delighted to help.