The planning and scheduling function is the heart and soul of the maintenance work management system. It is one of the fastest and most effective investments an organisation can make to improve productivity of its maintenance teams resulting in improved asset availability. Many organisations have documented processes and highly integrated Computerised Maintenance Management Systems (CMMS) but still have poor performance in areas of maintenance work management, especially planning and scheduling. What makes an organisation’s work management system efficient and effective is the competence of its people.
In my experience the factors that contribute the most to poor planning and scheduling performance are related to people’s competencies, including:
- Lack of good practices in work management and supporting IT systems.
- Lack of foundational knowledge within the maintenance leadership team. (Refer to our article “10 tips for better maintenance” for more on this topic.)
- Despite the required IT Systems skills, a lack of understanding of the end-to-end planning and scheduling process.
- An understanding of the value planning and scheduling adds to the business and how each individual contributes.
- Lack of understanding of IT systems functionality and how it can make the process more efficient as opposed to being a burden.
The first factor above is addressed by defining good practices in your work management process and then setting up complementary IT systems. The rest of the factors are usually addressed by training. Organisations therefore spend thousands of dollars a year on maintenance planning and scheduling training but does training ensure good application in the work environment?
Pathway to implementation
I was once asked by a trainee attending our Maintenance Planning and Scheduling Excellence course if there is a formal degree, diploma or trade certification in Maintenance Planning and Scheduling. Most of you would know the answer, “No”. So what’s the secret to being competent and to the implementation of good maintenance planning and scheduling? While most of you may be thinking that attending in-house or public training courses is the secret, in my experience it requires more. It also requires coaching.
Before I talk about maintenance planning and scheduling coaching, let me first ask you “How many training courses have you attended or arranged where you felt the learning objectives were fully implemented?” I am guessing only a few. As a trainer of maintenance planning and scheduling courses I always ask the participants for their feedback on the training, how the training will help in their organisation to improve and how they plan to implement what they have learned at their workplace. The first 2 questions are always simple for them to answer as it depends on my performance as a trainer and the quality of the course material, however, the 3rd question is always challenging. Below are the few interesting but true answers I have received when asking people how they plan to implement what they have learned at their workplace.
- My current workload doesn’t allow me to practise new skills.
- The training was great and now I know maintenance planning and scheduling fundamentals, principles and their benefits, but I still don’t know how to apply these in practice using my organisation’s processes, CMMS and other systems.
- I don’t know which transaction codes/tab/screen in my CMMS I need to go to generate a list of backlog/forward log, level resources, or to generate a weekly schedule.
- Can you please show me on my existing CMMS and using other tools how I can effectively and efficiently do most of the good things we learnt today?
- I had previously attended a full day CMMS training course and now through your training I finally understand the principles and fundamentals behind it. Can I contact you for any questions I may have when I apply learnings from these training courses?
From reading the above comments it is clear that training on its own will not help you put the learnings into practice; the secret to bridge this gap is “Coaching”. The figure below is a representation of the pathway to implementing high quality maintenance planning and scheduling practices, incorporating the often forgotten aspect of coaching.
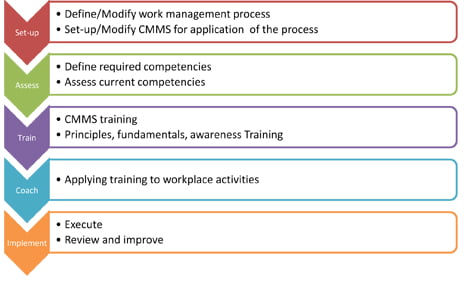
So, what is maintenance planning and scheduling coaching and how does it benefit you?
What is coaching?
Coaching is about helping and sharing knowledge to establish and embed new or modified processes within your current work context. Coaching provides a deeper understanding of why certain tasks and process should be followed and how to apply them within your specific organisation and job role. In general, the characteristics of one-on-one on the job coaching are:
- It is supportive rather than evaluative, meaning it guides the recipient rather than testing them
- It is collaborative in nature so it allows good discussion on key learnings
- It is observation-based and performance focused so it reveals gaps in understanding
- It shares ideas and practices
- It reduces the isolation that can sometimes be felt in a classroom environment
- It transfers learning from theory to practice
- It helps to assure high quality implementation of training
Our coaching system takes the shape of a typical plan-do-check-act cycle through regular contact with individuals as depicted below:
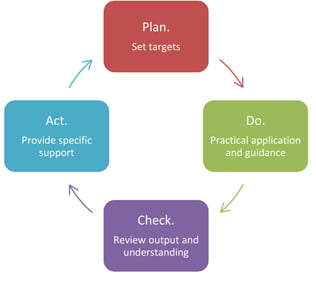
- Plan. First, plan for tasks ahead and set targets to be achieved in the next period.
- Do. Provide guidance on the execution of tasks but also provide the opportunity to put learnings into practice.
- Check. Check output, improvement and understanding at the next contact session.
- Act. And lastly provide specific support to address issues.
Focus of Coaching
The specific focus and activities of our maintenance planning and scheduling coaching sessions include:
- Support the integration of detailed production and maintenance plans on a daily, weekly and monthly basis.
- Support the establishment of detailed plans for individual maintenance activities (repairs and services) which detail the job procedures including safety, environmental, quality assurance checkpoints, associated standards, equipment downtime, labour, parts and materials, other resources required and any other considerations required for the successful completion of each individual job.
- Supporting the creation of formal daily and weekly maintenance plans and schedules which outline the jobs to be performed, the timing of those activities, and balances the work scheduled with the availability of labour, equipment, and other resources required for the performance of the work.
- Coaching in the setting of priorities for all new work orders as they arise, and the reprioritisation of work orders on a weekly basis.
- Support increasing the visibility of production and maintenance plans and schedules throughout the maintenance and production departments, and ensuring a highly visible communication of the achievement of the plan.
- Assessing the competency of the participant and identification of gaps that can be addressed through specific interventions or further coaching sessions.
Outcome
The below comments are a few of the testimonials we have received from participants while coaching them in their work management process steps and tools:
So this is what you meant about critical path management and resource levelling in the training course. I know now how I can manage this using our MS Excel tool.
In the past we had lots of jobs cancelled or rescheduled due to poor communication between the planning team and the maintenance and production teams. I will ensure my future work packs contain all critical information to avoid some of these issues in the future.
The new agenda that you helped me develop for our weekly planning meeting is great. This helps me discuss maintenance conflicts, review labour availability and track material availability.
Clearly coaching helps participants to practice learnings from training in their work environment and gives them further opportunity to discuss issues, ask questions and use new skills while conducting their regular tasks. Some of the numerous benefits from these one-on-one coaching sessions include:
- Identification of external issues which planners and scheduler face in real life, including a limited number of resources, ineffective maintenance strategies, poor spare parts availability, etc.
- Application of maintenance planning and scheduling principles using in-house processes and tools, and consequently achieving improvements in the efficiency, effectiveness and safety of maintenance tasks which may arise from diverse areas such as reduced spares costs, reduced rework and improved equipment reliability.
- Assessing the competency of the participant and identifying gaps that can be addressed through further training and coaching.
- An opportunity for the participant to coach and mentor others from their experience.
Conclusion
There is more to the successful implementation of maintenance planning and scheduling than just sending your people to training courses. Coaching provides a highly effective way of achieving a step change in the performance of your planning and scheduling function.
If you would like to take up the opportunity to engage us with a review and development of your maintenance work management process or CMMS, competency assessment, training and coaching for your personnel, please contact one of our highly experienced work management specialists.