Acquiring a new plant should be exciting. But what if the smooth handover you expected turns out to be a maze of missing maintenance plans, poor-quality asset registers, and unclear data ownership?
It happens more often than you’d think—even when the seller is a reputable, Tier 1 operator.
Operational readiness often gets overlooked until the ink is dry on the contract of sale. By then, it’s too late. Critical information gaps force rushed decisions, maintenance strategies stall, and the risk to equipment reliability skyrockets. We’ve seen it firsthand.
In this article, I’ll share how we navigated these challenges during a recent brownfield site acquisition, the techniques we used to get back on track, and what steps you can take now to avoid these pitfalls altogether.
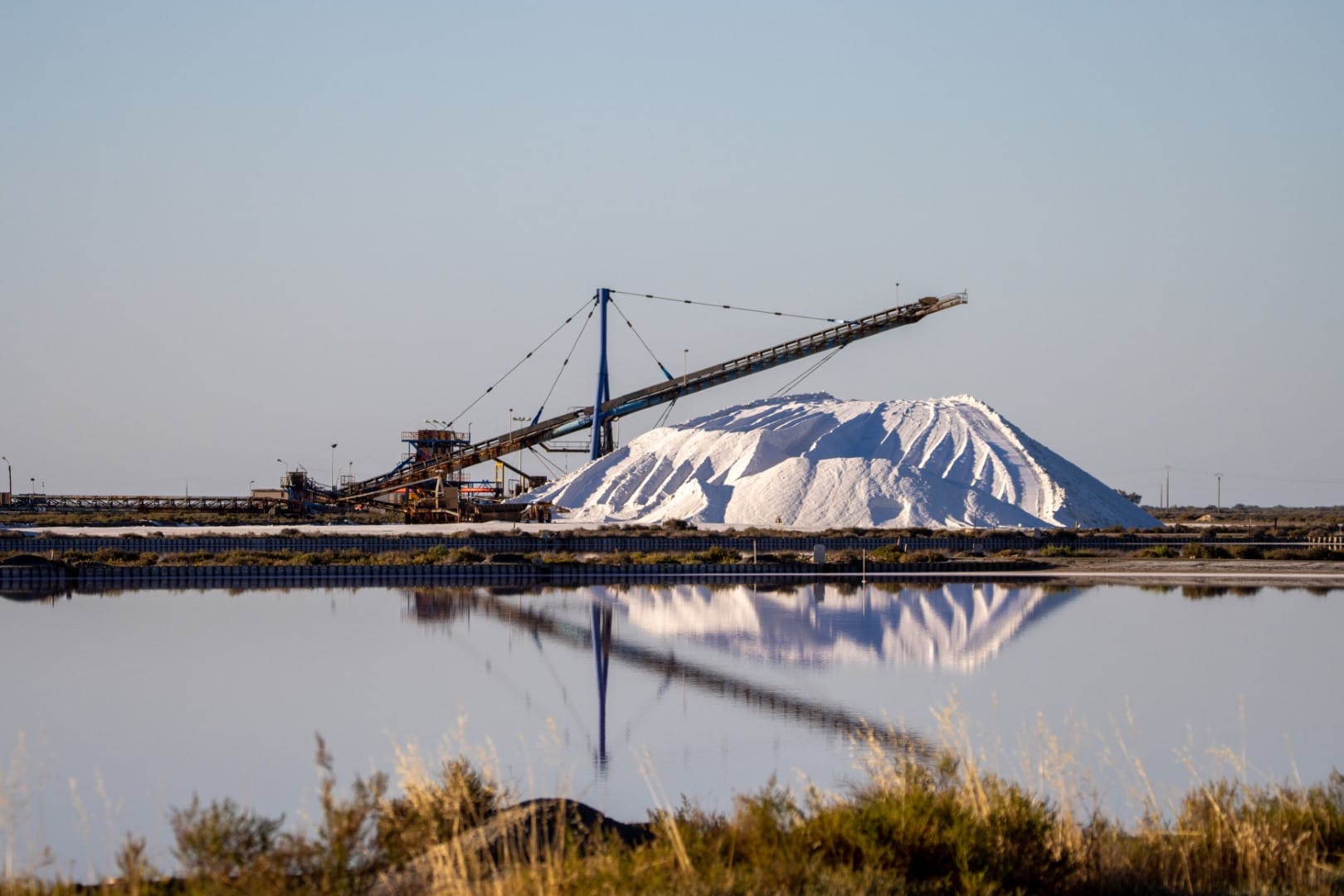
The Challenge: Data Gaps and Shifting Timelines
Assuming that comprehensive asset registers and maintenance records will be handed over is a costly gamble. In our case study, the anticipated clarity turned into confusion when:
- Data Gaps
- Incomplete asset registers and incomplete materials lists forced teams to rebuild vital information almost from scratch.
- Critical maintenance plans were missing, undermining the reliability of the plant from Day One.
- Shifting Timelines
- Government approvals and unexpected delays shifted go-live dates, adding pressure on teams to deliver under ever-changing conditions.
These challenges threatened not only the maintenance management system but also the broader asset management strategy.
Agile Solutions: Turning Crisis into Opportunity
Facing data deficits and compressed schedules demands a nimble, proactive approach. Here are some of the key strategies we deployed:
- Flexible Prioritisation
- We mapped out scenarios each day, asking: “What do we have, what can we expect, and how critical is each task?”
- High-value tasks were sometimes postponed until better data was available, while smaller, impactful improvements kept progress steady.
- Machine Learning for Materials Classification
- Instead of manually classifying over 16,000 items – a task estimated to take a year – we used targeted machine learning techniques.
- By manually labelling a training set and then leveraging the model, we classified the bulk of the materials in mere weeks, dramatically reducing turnaround time.
- Agile Collaboration and Contingency Planning
- Frequent stakeholder meetings and short work cycles ensured that any unexpected information was quickly addressed.
- Backup plans were in place for every scenario, minimising risks when timelines shifted.
Lessons for Asset and Maintenance Management
This experience taught us that operational readiness must be woven into your asset management strategy from the outset. Here’s what to take away:
- Data Is King
- Verify and secure all relevant data—including financial and non-financial asset registers—early in negotiations.
- A robust data governance framework can prevent costly delays and ensure smooth transitions.
- Challenge Assumptions
- Even reputable Tier 1 operators can leave behind data gaps. Scrutinise every assumption about process maturity and maintenance records.
- Questioning the status quo can help you pinpoint and resolve blind spots before they escalate.
- Leverage Technology Wisely
- Don’t be seduced by flashy AI without considering practical outcomes. Targeted machine learning can deliver results fast, but large language models might not be the best fit for every classification task.
- Use technology to enhance your maintenance management system, not to replace sound judgement.
Conclusion
Operational readiness isn’t just a box to tick—it’s the foundation of reliable asset management and efficient maintenance management systems. By recognising data challenges early, embracing agile solutions, and challenging every assumption, organisations can turn potential pitfalls into opportunities for improvement. The result is a more resilient and proactive approach that optimises preventive maintenance and reliability centred maintenance from Day One.
Take a moment to reflect. Are you confident in the quality of your asset data? Are your systems and processes truly ready for the day you take control—or are there hidden gaps waiting to surface?
If you’re unsure or simply want a sounding board, contact us now to talk to one of our expert consultants.
Do you need help establishing Asset Management and Maintenance Management processes, systems and data for a new operation?
We have a team of specialist consultants ready to help. Speak with one of them today, or read more about our services below.