In the previous article in this series we offered the view that assuring equipment reliability is a critical business activity, with potentially serious safety, environmental and economic consequences if it is not achieved. We also expressed the opinion that reliability is everybody’s responsibility. However, this view is only useful if clear accountabilities are established for reliability in each stage of the asset life cycle. Otherwise we potentially fall into the trap (often expressed in notices in communal lunchrooms) of the story of four people, named Everybody, Somebody, Anybody, and Nobody:
- There was an important job to be done and everybody was sure that somebody would do it.
- Anybody could have done it, but nobody did it.
- Somebody got angry about that because it was everybody’s job.
- Everybody thought that anybody could do it, but nobody realized that everybody wouldn’t do it.
- It ended up that everybody blamed somebody when nobody did what anybody could have done.
In this article, we will explore the key organisational accountabilities that should be in place for effective consideration of reliability during the design phase of the asset life cycle and the roles that different organisational functions can play in supporting reliability in design. In addition, we will discuss the importance of incorporating reliability considerations during the design phase of the asset life cycle.
Please note that reliability in design is an extensive subject. This article, due to space limitations, provides an introductory overview of the key elements. Nevertheless, I hope that there will be some practical guidance in here for those who may be less familiar with this subject.
Articles in this series
Why is reliability in design important?
An item’s reliability assures us that an item will function as intended without failure for the desired periods during its design life. From a business perspective, it ensures that we have viable business operations in producing the product or service required.
Consequently, failures can cause one or more undesired events:
- Safety Incidents – injuries or death of personnel
- Environmental Incidents – local or major
- Impact on reputation – safety and environmental incidents in particular can greatly affect a company’s reputation which in turn can impact sales and company revenue
- Breaches of the law – by not meeting required standards and operating licence conditions. Applies particularly to safety and environmental incidents.
- Production Losses – downtime caused by the failure and then the need for maintenance
- Increased Costs – through the need to do rework or early replacement by reduced life
If we consider the asset life cycle, as illustrated in Figure 1, we can see that decisions made in each phase (including failure to complete required activities) can have significant effects on later phases. One of the main objectives of an effective, holistic asset management system is to ensure these linkages are understood and decisions are taken with this knowledge in mind, ie. to prevent the “dead cat over the wall” mentality.

In terms of reliability, this is particularly true. Decisions made during the Concept, Design & Install phases of the Asset life cycle determine a fundamental baseline level of reliability which generally cannot be exceeded during the Operate & Maintain phase without considerable effort and expense.
This is often illustrated graphically in a cost influence curve in Figure 2. This illustrates the general concept that our ability to influence the total cost of a project is greatest earliest in the project – before most of the expenditure has taken place. And this is also true when discussing the costs associated with generating a desired level of reliability.
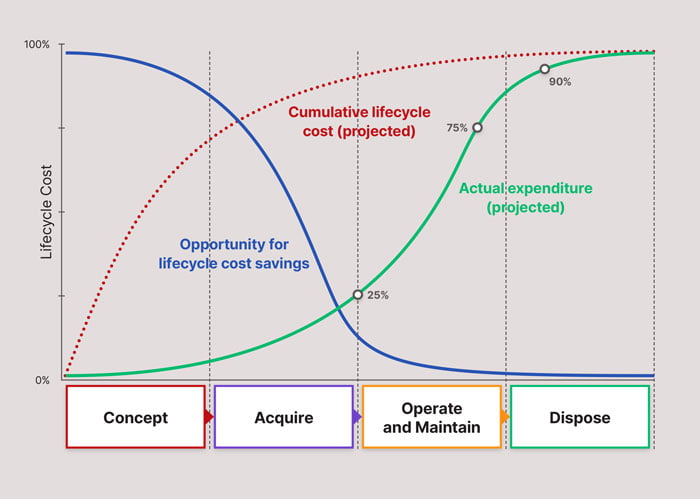
Determining the reliability required of an asset during the design phase
The level of reliability of an asset, as determined by its fundamental design (and installation) is often termed its “Inherent Reliability” (see MIL-HDBK-338B: Electronic Design Reliability Handbook). This generally makes assumptions regarding operating and maintenance conditions and practices that will exist after the asset is installed and commissioned. The Inherent Reliability required of the asset is generally used as the primary basis for design decisions.
Inherent Reliability (the level of reliability of an asset, as determined by its fundamental design and installation) differs from “Operational Reliability” which is the reliability of the asset actually observed in operation. It goes without saying that if actual operating and maintenance conditions and practices vary significantly from those assumed by designers then Operational Reliability will vary significantly from Inherent Reliability. It is vital, therefore, that the assumption that designers make during the design phase regarding actual operating conditions and practices are as accurate as possible.

How is this Inherent Reliability determined? In the ideal world, the starting point would be (in line with the requirements of ISO 55001, the international standard for Asset Management) the organisation’s overall objectives. In practice, however, there is a trade-off between asset performance or benefits (such as reliability or capacity), costs and risks, as illustrated in Figure 3. The optimum point will depend on a number of factors, such as your organisation’s attitude to the acceptance of risk. It should be noted that there is, in fact, an additional dimension (not illustrated) to Figure 3 – that of time. Requirements in terms of costs, asset performance and risks may vary over time, and ideally these should also be taken into account. The situation gets even more complicated when you consider that most larger capital projects involve the design, installation and commissioning of multiple assets which together make up an asset system. The interaction between these individual assets can often impact on the reliability of the system as a whole.
Systems engineering as an approach for assuring reliability in design
To take account of these complexities, a Systems Engineering approach can be used to minimise the risk of an inappropriate design being put in place. This is a comprehensive approach to the determination, specification and verification of asset systems, and a detailed exploration of Systems Engineering is beyond the scope of this article. As a very brief summary, however, one of the key concepts in this approach is the Systems Engineering “V”, as illustrated in Figure 4.
On the left-hand side of the V, various activities are taken to ensure that business requirements are cascaded down through the various levels of detail in design and taken into account in the design process. We will discuss some of the tools and methodologies that may be used as part of this process later in this article. On the right-hand side of the V, verification activities take place to validate that the designs put in place actually deliver the performance expected.

However, when it comes to reliability, this conceptual arrangement will only work if the required level of reliability is actually specified as a business requirement. In some industries, this element of asset performance is often overlooked (in our experience), with specifications focusing largely on capacity, cost (and occasionally availability). It goes without saying that if the desired level of reliability is not specified then the organisation will “get what it gets” in terms of reliability, and this may or may not be acceptable.
It is also important to validate that, where reliability requirements are specified, that these are actually achieved. While some industries and some organisations do this quite well (incorporating statistical analysis and formal reliability testing methods into their acceptance processes), for many organisations (yes, I am talking to you in the mining industry), a simple “will it run for more than a day without failing” is the only test that is applied. For critical assets, this is simply not good enough, and represents a significant opportunity for improvement.It is worth noting that, for many organisations, designs incorporate standard components or equipment items that are produced by third party manufacturers. While the inherent reliability required of these components should, ideally, be specified during the design, manufacturers may be reluctant to share the reliability data obtained for their products with their customers. Indeed, as mentioned earlier, the inherent reliability achieved by an item depends, to a large extent, on the assumptions made regarding the operating conditions and practices to which the item will be exposed. The assumptions made by the designer may well be different to those made by the manufacturer, and so manufacturer data in this area, even if provided, may not be applicable for your situation. Unless you are prepared to incur the time and expense with performing reliability testing of these items for your particular situation, then it may well not be practical to determine in advance the reliability performance to be achieved for every item that you purchase. At best, you may be able to estimate the expected reliability, based on results achieved in practice in other installations (including in your own operations). Nevertheless, the decision to forego specification and verification of reliability for items incorporated in a design should be a conscious one, rather than an unconscious one or an error of omission.
There are a range of tools and methodologies that can assist with specifying, validating and verifying reliability during the design phase. We will discuss these (and other reliability tools) in a later article in this series.
Roles and responsibilities for reliability in design
As we have seen earlier in this article, the design and construct phase of the asset life cycle is the most important when it comes to assuring reliability in operations. Decisions made during this phase cannot easily be undone or changed during later stages. In fact, decisions made during the design phase are too important to be left solely to designers to make! It is important to realise that, for all their strengths and experience in engineering design and construction, most project engineers and designers do not often have sufficient operational experience to be able to fully understand and appreciate the impact on operations of the design decisions that they make. Furthermore, once an engineering project is completed, they are rarely given the opportunity to experience their design in operation, and are even more rarely given feedback on the operational reliability that results from their design decisions.
While overall accountability for reliability in design must rest with designers and project engineers, other functions within the organisation have a vital role to play in assisting them to achieve the overall reliability goals that the organisation is seeking. So, what are the key roles that organisational functions have in supporting reliability in design? Some of the key activities for different organisational roles are outlined below.
Designers / project engineering
- Ensure that required reliability performance, especially for critical assets, is explicitly included in specifications for systems, equipment and/or components
- Ensure that Systems Engineering is used to not only ensure that reliability performance is accurately specified and validated, but that the actual reliability performance achieved can be (and is) verified.
- Make appropriate use of quantitative and qualitative techniques to support and guide design decisions that have an impact on reliability.
- Seek input from those with operational experience to ensure that assumptions made regarding operating conditions and practices during the design phase are valid
- Perform sensitivity analysis to understand the potential reliability impact of variation from the assumed operating conditions and practices – ensure that the design is robust enough to cope with reasonable variation in key parameters
Senior management / finance
- Ensure that capital funding decision-making adequately assesses asset reliability performance, as well as initial capital cost – a whole-of-life costing model should be adopted
- Ensure that sufficient funding is allocated in the early stages of a project to adequately assess and, if necessary model, alternative solutions from a reliability perspective
- Ensure that all organisational functions are engaged in the Asset Design process, and that sufficient resources from operational and other support functions are allocated to the project
- Ensure that Procurement decision-making processes are aligned with the achievement of maximum overall asset value, not cost-reduction
Operations and maintenance
- Ensure that operations and maintenance resources and data required to support effective decision-making during the design phase are provided as and when required. In particular, during the early stages of a project. One of the biggest complaints we hear from project engineering teams is that even when invited, operations and maintenance personnel don’t attend meetings and don’t get involved early enough in projects – often only getting serious when asked to attend a final design review – by which time the opportunity to make changes to designs is limited.
- Ensure that the assumptions made by asset designers regarding operating conditions and practices are reasonable.
- Collect and provide accurate data regarding asset performance (throughput, efficiency, uptime) for existing assets that may be usefully included in simulation models during the design phase for new assets
- Collect and provide accurate data regarding asset reliability and associated failure modes for existing assets that may be usefully included in reliability models during the design phase for new assets
Procurement
- Ensure that procurement decisions provide maximum overall value, rather than lowest price.
- Ensure that reliability is explicitly included as a performance requirement in acquisition of all critical equipment, and that claimed reliability performance is verified (if necessary using formal testing) before equipment acceptance
Conclusion
This article has outlined some of the key considerations for reliability during the design phase of the asset life cycle. If you would like to receive early notification of publication of these articles, sign up for our newsletter now. In the meantime,if you would like assistance in establishing effective consideration of reliability in design within your organisation, please contact me. I would be delighted to assist you.