As consultants, we have seen our clients spend an awful lot of time performing detailed analysis in order to determine the criticality of their equipment. In our view, much of that time is unnecessary. In this article, we will explore a streamlined approach for determining equipment criticality, which achieves the desired results, but more quickly, and consuming less of your most valuable people’s time.
Before starting, however, it is worth first considering whether you need to perform Equipment Criticality Analysis at all, and if you do, what you are going to use the resulting outputs for. As we discuss in the article “Equipment Criticality Analysis – Is it a Waste of Time?”, there are a number of possible uses for Equipment Criticality Analysis, some more sound than others. It is important to start this process with the end objective clearly in mind – there is definitely nothing more wasteful than spending lots of time assessing the criticality of every asset in your organisation, loading this into your ERP, EAM or CMMS system, and then doing nothing with it.
In essence, the key steps in performing Equipment Criticality Analysis are:
- Agree on the Risk Matrix to be used
- Assemble your equipment/asset hierarchy
- Assess the Failure Risks associated with each asset/equipment item
Agree on the risk matrix to be used.
The starting point here is most likely to be your corporate risk matrix. However, you should bear in mind that your corporate risk matrix may need to be modified to suit its application for equipment criticality assessment. These modifications will most likely be required in two areas:
- As the size of the risks associated with failures at an equipment level are generally are lower than those assessed at a corporate level, the trigger levels for each level of consequence will most likely need to be lowered in order to provide a better “spread” of results. For example, your Board of Directors may consider (at a corporate level) an event which leads to a loss of revenue of $1m to be “Moderate” or “Minor”, but at a plant or operation level, this may be more likely to be “Significant” or “Major”.
- Corporate risk matrices, in my experience, tend to contain a lot of risk categories that overlap. For example, we have seen risk matrices that assess individually against all of the following categories – Compliance, Health, Safety, Environmental, Community, Reputation. In reality, at equipment level, if an event leads to significant consequences in one of these categories, then it will most likely also have significant consequences in one or more of the other categories. There is, therefore, often an opportunity to combine or delete consequence categories in order to speed the analysis.
Assemble the equipment/asset hierarchy.
If your equipment hierarchy is established along functional lines (for example, a plant is made up of a number of process units, and each process unit is made up of several equipment systems, and each system is made up of individual equipment items etc.), then this will greatly speed equipment criticality analysis (for reasons we will discuss later in this article). If your equipment hierarchy is not organised along these lines (if, for example, it is just a “flat file” of equipment items, or if the hierarchy is arranged along equipment class lines), then it is worth spending some time restructuring the hierarchy along functional lines.
Even if your hierarchy is arranged along functional lines, however, frequently there is a need to review the structure. We often find anomalies – equipment items with no parent, or items located in the incorrect position in the hierarchy. Fixing these up before you start will speed equipment criticality analysis later.
Assess the failure risks associated with each asset/equipment item.
When assessing the failure risks to determine equipment criticality, there are four key tips for achieving a robust, but streamlined process.
- Realise that risk relates to events – not equipment
- Select only one event – the Maximum Reasonable Outcome (MRO) event
- Assess only one risk dimension – the one with the highest level of risk
- Start at the top of the equipment hierarchy and work down
We will discuss each of these in turn.
Realise that risk relates to events, not equipment.
The risk assessment process, according to ISO 31000:2009 Risk management – Principles and guidelines consists of three key steps:
- Risk Identification
- Risk Analysis, and
- Risk Evaluation
There are two key things to note about risk. First, risk relates to events. Second the risk associated with each event can be evaluated by assessing the likelihood of that event, and the consequences associated with that event (normally visualised in the form of a risk matrix, as illustrated below).
So what are the implications of this for determining equipment criticality?
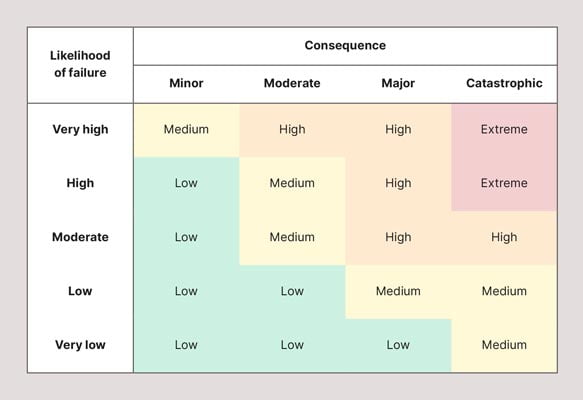
Select only one event: the maximum reasonable outcome (MRO).
First, there are a range of potential failure events that could be associated with an equipment item, and the risks associated with each event will be different. Does that mean that we need to identify every possible (or even likely) failure event associated with each equipment item? Clearly not – as this would be particularly time-consuming, and not particularly useful. So which event (or events) should we choose? We recommend selecting only one event – an event which represents the Maximum Reasonable Outcome (MRO) in terms of risk for the equipment item. In other words, we are looking for an event that is at least plausible in terms of likelihood, but for which the overall risk is believed to be highest.
Clearly different individuals will have differing views regarding what that event should be, and so I strongly recommend that the entire risk assessment process be undertaken in a workshop environment, with input from those who understand the equipment best, and who understand, from a business perspective, the consequences of equipment failure. As a minimum, this will require the involvement of production/operations and maintenance personnel, but may also require the involvement of other specialist support roles, such as safety and environmental advisers. For the same reasons, to avoid potential confusion (and to aid the future update of the criticality assessment) the MRO event that has been agreed upon should be clearly documented.
Second, for any one failure event, there are a range of possible outcomes. Further, as the likelihood and/or consequence of each event can vary over time, and can also be different if we are assessing unmitigated risks compared with the risks with risk mitigation actions in place, we need to be clear about over what time period we are assessing equipment criticality, and why we are performing this assessment. Again, the team should focus on (and the workshop facilitator should document) the MRO outcome and any associated assumptions for their chosen event.
Assess only one risk dimension: the one with the highest level of risk.
In addition, most corporate risk matrices assess risk on multiple dimensions – Safety, Environment, Production, Cost, Reputation, etc. Assessing each event against every one of these dimensions is generally a waste of time. When we are assessing equipment failure risks, it is most often the event with the greatest risk that we are interested in, and it is generally pretty obvious which dimension will give that highest level of risk. For example, if we were assessing the criticality of a pressure relief valve in an oil refinery, the safety risks are most likely to be those of most interest to us. Alternatively, if we were considering the failure risks associated with failure of the one and only electrical incomer into our plant, the economic risks associated with lost production are most likely to be of greatest interest. I have seen plenty of people waste plenty of time assessing every risk dimension on every equipment item (and even come up with complex formulae to calculate the “average” risk based on all of these assessments), and I can advise strongly against such an approach – it does not lead to better decisions.
Start at the top of the equipment hierarchy and work down.
In order to streamline the decision-making process further, I suggest that you start at the top of the equipment hierarchy and work down. If you follow this process, then you will find that, by definition, equipment items at a lower level in the hierarchy cannot have a higher criticality than the item above it. Therefore, once you have identified an equipment item in the hierarchy where the overall criticality rating belongs in the lowest category, all items below it must also belong in this category, and there is no need to evaluate the criticality of those items. Following this approach reduces the number of decisions to be made. But note that, for this approach to work, this requires a robust and accurate equipment hierarchy in the first place (as discussed earlier in this article).
I trust you have found the approach outlined above useful, and the tips helpful. If you have any comments or questions, please do not hesitate to contact us.