One of the greatest frustrations for many reliability engineers and maintenance managers is that they struggle to obtain the funding that they believe they need to implement their improvement strategies. However, for senior executives to incorporate reliability improvement as a core element of their strategic plan and their budgets, there must be a sound business case.
As technical personnel, this means that we need to talk in the same language that senior executives do; we need to convert technical language into financial terms.
The primary purpose of any for-profit organisation is to maximise total shareholder return within a tolerable level of risk. These organisations achieve this by maximising Economic Value Added (EVA).
What is Economic Value Added?
Economic Value Added (EVA) is a measure of the superiority of the return a company is able to realise on invested capital above the baseline return expected by the investment community. Positive EVA means the organisation will add value for shareholders; negative EVA means they would be better off if management just gave them the money as a dividend.
One model that can assist in helping “for profit” organisations to understand where the opportunities are to maximise EVA is the Economic Value Added driver tree. The EVA driver tree breaks EVA down into various subcomponents and then adding, subtracting or dividing these components by each other in order to derive overall EVA. An example of an EVA driver tree with some sample data is illustrated in Figure 1, sourced from publicly available records of a major mining company.
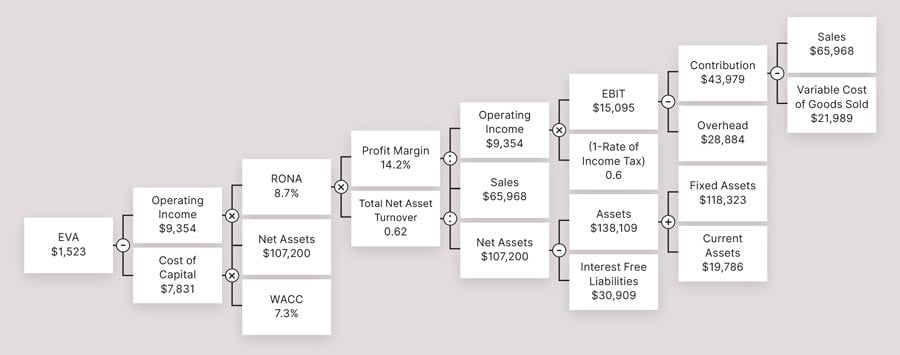
From this tree, we can see that EVA depends on:
- Sales revenue (more is better)
- Variable and fixed costs (less is better)
- The value of assets employed (less is better)
- The Weighted Average Cost of Capital (WACC) (less is better)
- This in turn depends on: the extent to which the company is seen as being “risky” (investors and lenders to higher risk companies require a higher rate of return), and
- The ratio of debt to equity funding (debt is cheaper).
What has this got to do with maintenance and reliability?
Maintenance and reliability improvement can focus on two areas:
- Maintenance Effectiveness
- Doing the right things at the right time
- Predicting and Preventing equipment failures
- Improving equipment reliability
- Maintenance Efficiency
- Doing things right
- Maximising maintenance labour productivity
- Minimising parts and materials costs
These can add value for shareholders in the following ways.
Improving maintenance effectiveness can:
- Improve Overall Equipment Effectiveness (OEE) for equipment, therefore generating additional sales with no further investment in capital equipment required
- Reduce operating costs, improving EBIT
- Improve product quality, increasing sales price
- Defer the need for additional capital expenditure
- Reduce operating, safety and environmental risks
Improving maintenance efficiency can:
- Reduce maintenance costs, improving Earnings Before Interest and Tax (EBIT)
- Also have some positive impact on Overall Equipment Effectiveness (OEE)
The impact of increasing equipment availability
Overall Equipment Effectiveness (OEE) can be calculated using the following formula:
OEE = equipment availability * utilisation * production rate * quality rate
Better maintenance and reliability can increase equipment availability by:
- Preventing or eliminating breakdowns
- Improving the mean time to repair
- Reducing the duration of planned shutdowns
It can also improve production rate and quality rate by ensuring that equipment is capable of producing at maximum capacity, with no defects.
We can model the potential impact of increasing OEE by feeding this into our EVA Driver tree. Let’s assume that we can increase OEE by 1%. What would the impact of that be on EVA?
Increasing OEE (assuming that we can sell all the additional product we make at the same price) drives sales revenue up by 1%. But it also drives up our Variable Cost of Goods sold by 1% – we need to buy more raw materials and/or increase energy/reagent costs as a result of the increased production output.
Feeding this into the EVA model, using the sample data shown, indicates that a 1% increase in OEE in this case leads to an 18% increase in EVA (and potentially an 18% increase in share price). Pretty impressive. This is illustrated in Figure 2.
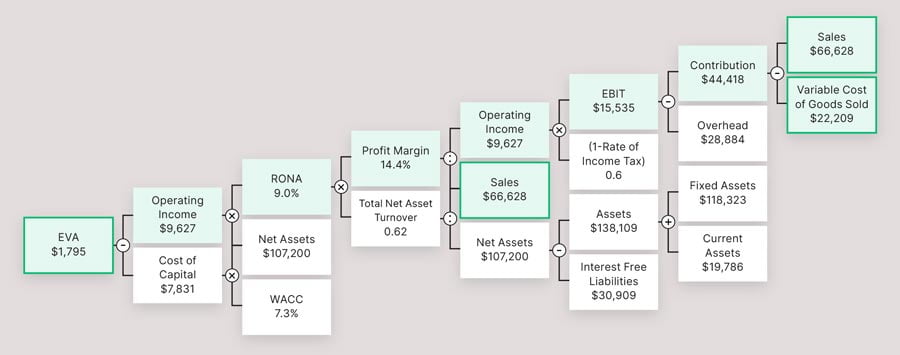
The impact of reducing operating costs
Better maintenance and reliability can have a positive impact on operating costs by:
- Improving the reliability of equipment, thereby reducing start-up and shutdown costs
- Improving the efficiency of equipment, thereby reducing energy and reagent costs
We can also model the potential impact of reducing operating costs by feeding this into our EVA Driver tree. Let’s assume that we can reduce operating costs by 1%. What would the impact of that be on EVA?
Feeding this into the EVA model, using the sample data shown, indicates that in this case a 1% reduction in Variable Operating Costs, in this case, leads to an 4.4% increase in EVA. Not quite as impressive as the gains to be obtained from increasing Overall Equipment Effectiveness, but still worth having – especially if it is easier to reduce operating costs than to increase OEE. This is illustrated in Figure 3.
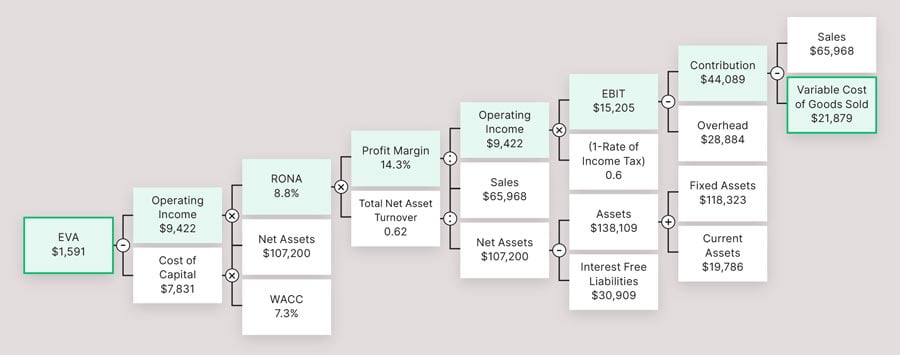
The impact of better product quality
Improving the reliability of critical equipment can permit fewer “off-spec” excursions that negatively impact on product quality. It can also assist with reducing the variability of product quality, thereby either:
- Reducing blending and rehandling costs, or
- Permitting the achievement of tighter product quality specifications, which may be able to be sold for a higher unit price.
Let’s model the financial impact of being able to increase our sales price by 1% due to better product quality. In this case, using our sample data, it leads to a 27% increase in EVA. Wow! This is shown in Figure 4.
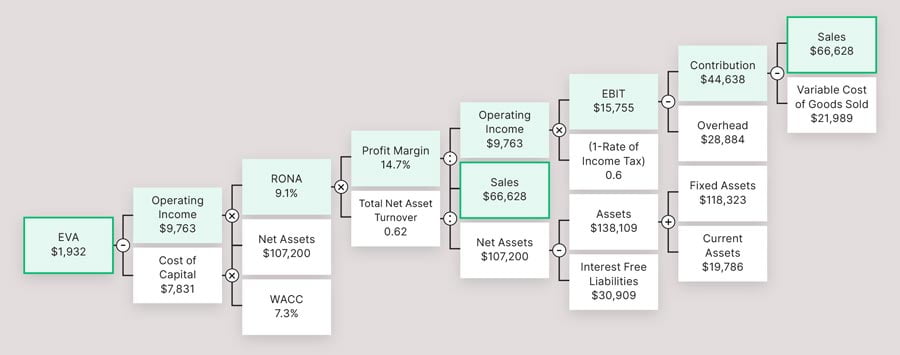
The impact of deferring capital expenditure
Better maintenance can assist in deferring capital expenditure by:
- Ensuring that equipment is properly maintained – thereby extending its life
- Maximising the availability, reliability and throughput rate of the equipment – so that the need for additional productive capacity is deferred.
Let’s say we reduce the value of our fixed assets by 1% as a result of these initiatives. Figure 5 shows that EVA increases by 6% on this occasion.
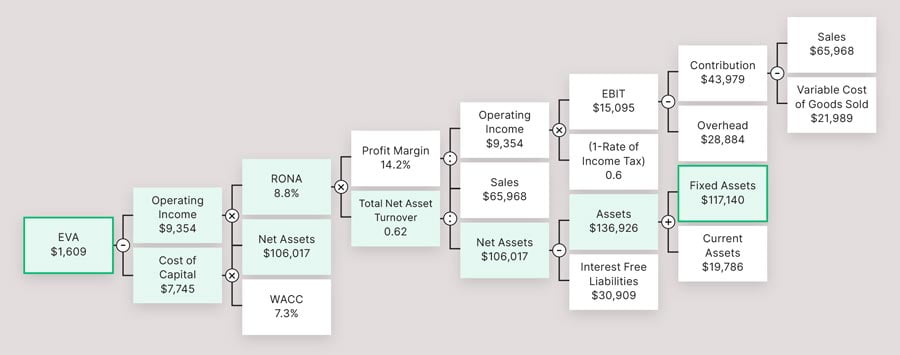
The impact of reducing operational, environmental and safety risks
Better maintenance can reduce the overall level of risk within an organisation by:
- Predicting, and avoiding catastrophic failures
- Ensuring that all environmental and safety related equipment and systems are fully operational when required
The impact of this on EVA is indirect. In the EVA model, you can see that EVA depends on the Weighted Average Cost of Capital (WACC). However, WACC in turn depends on several other factors – it has its own driver tree as shown in Figure 6.
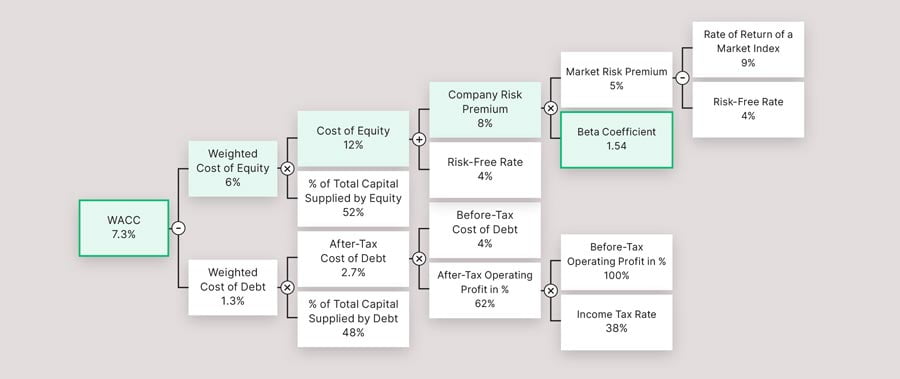
Of particular note in this driver tree is the element “Beta Coefficient”. This is a measure of a share’s price volatility in relation to the rest of the market. In other words, how the share’s price moves relative to the overall market. Stocks that have a beta greater than 1 have greater price volatility than the overall market and are more risky.
Risk also implies return. Shares with a high beta should have a higher return than the market. If you are accepting more risk, you should expect more reward.
There are numerous examples where equipment failures have led to a negative impact on share price and greater volatility. Most notable amongst these is the share price of BP in comparison to one of its competitors (Exxon) and the overall market (Dow Jones Industrial Average) in the leadup and aftermath of three major equipment failures that it experienced, at Texas City, Prudhoe Bay and Deepwater Horizon. Figure 7 clearly shows this.
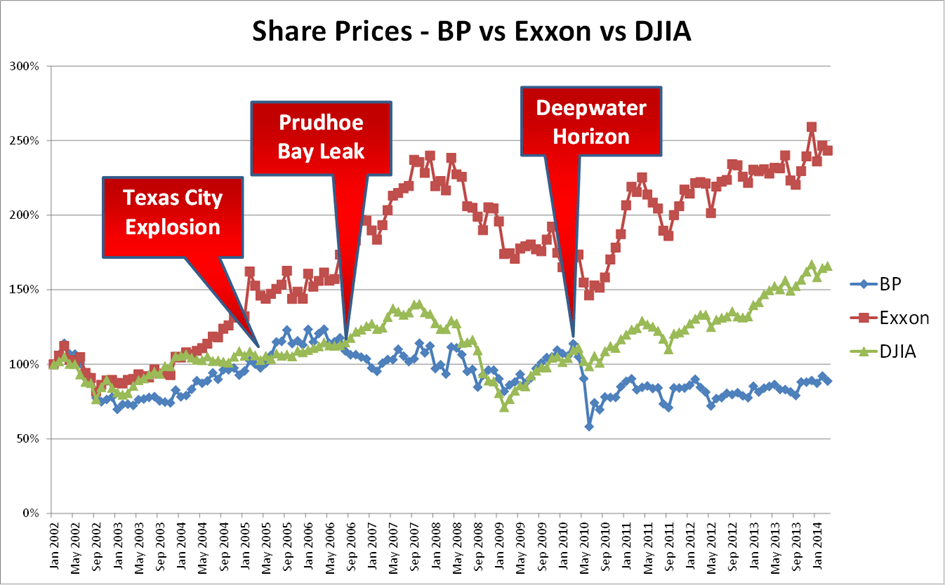
If, through better maintenance and reliability practices, we were able to reduce the Beta Coefficient by 1%, we can feed this into the EVA driver tree and we can see that this would result in an increase in EVA of 3%, as shown in Figure 8.

The impact of reducing maintenance costs
Last, but not least, let’s evaluate the impact on EVA of reducing maintenance costs. Maintenance can reduce its costs by being more efficient in its activities through improvement initiatives such as:
- Improving the quality of maintenance planning
- Being more thrifty with spare parts
- Improving the cost-effectiveness of the use of contract labour
- Etc.
Let’s be really confident, and see what the impact of reducing maintenance costs by 5% would be – assuming that these represent around 25% of variable operating costs. In this case, the impact would be an increase in EVA of only 4%, as shown in Figure 9.
This provides a much lower benefit than those that the modelling predicts from the other focus areas.
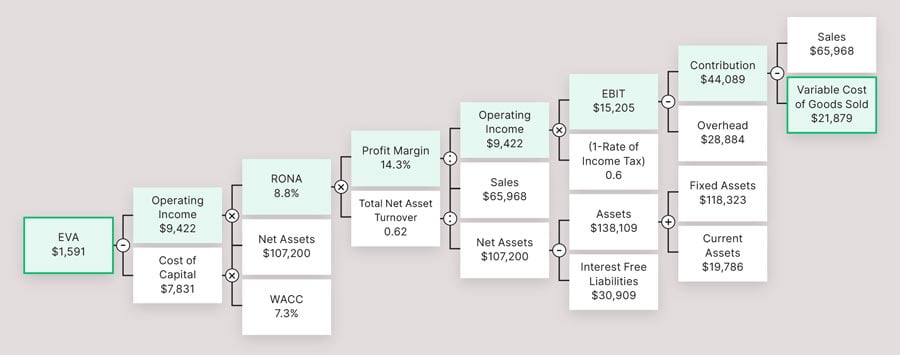
The dangers of a focus on cost reduction
Good managers should be aware that costs are an output from a process, not an input. Focusing on cost reductions, without identifying the specific process improvements which are to occur can lead to adverse, unintended consequences.
More specifically, the easiest way to reduce maintenance costs (and the option taken by many managers when under pressure to reduce costs) is to simply defer major maintenance activities to a future period. This does not eliminate the need to spend the money – it simply defers it. And it introduces several risks, not the least of which include the risk that:
- A much greater sum of money may be required to restore the equipment to operable condition in future
- The equipment may fail in the meantime, with associated impact on sales revenue, safety and environmental performance.
Summary of sample EVA modelling
In summary, our sample EVA modelling indicated the following increases in EVA.
Focus area | Improvement in EVA |
---|---|
Increase OEE by 1% | 18% |
Reduce operating costs by 1% | 4% |
Increase selling price by 1% | 27% |
Reduce fixed capital by 1% | 6% |
Reduce beta coefficient by 1% | 3% |
Reduce maintenance costs by 5% | 4% |
We saw that better equipment reliability can:
- Improve OEE for equipment, therefore generating additional sales with no further investment in capital equipment required
- Reduce maintenance costs, improving EBIT
- Reduce operating costs, improving EBIT
- Improve product quality, increasing sales price
- Defer the need for additional capital expenditure
- Reduce operating, safety and environmental risks
Are there any other areas of business activity that have such far-reaching impact?
Conclusion
Increasing asset performance by improving equipment reliability is a wide-reaching, and potentially huge driver of shareholder value – much greater than the returns to be obtained through cost reduction. However, we should note that maintenance cannot achieve this improvement on its own – it requires a focus on reliability improvement by the entire organisation.
Amongst our clients, those organisations that have realised the potential benefits of reliability improvement and a holistic approach to asset management, and are mobilising to achieve full organisational potential are already achieving significant benefits.
If you are considering a reliability improvement initiative, consider speaking to us to discuss how we might be able to assist you. Some of our areas of expertise are listed below.