“The best preparation for good work tomorrow is to do good work today.”
Elbert Hubbard
At some point in time, many organisations will undertake a review of their maintenance program. The reasons and aims of the review are various but in general they mainly come about as a result of some real and/or perceived deficiencies or excesses in the existing program. The desire is always to produce an optimised program that minimises waste, ie. make sure we are doing the right work at the right time. The ways and means of doing a maintenance program review are varied, however, in all cases the review will require resources, both in personnel (whether internal, external or both) and their time. This use of resources in turn equates to a cost to the business. Optimising your maintenance program will produce benefits, however, these benefits, the return on your investment, will only be realised once the new revised optimised maintenance program has been implemented.
A lot of diligent effort usually goes into the planning and execution of the actual maintenance review (perhaps using an RCM based process), however, what is often neglected to some extent, or often underestimated, is the amount of effort required to actually implement this new revised optimised maintenance program. Implementation includes the following activities:
Grouping and sequencing the right tasks into preventive maintenance routines
In the process of reviewing your maintenance program, you’ve concluded that certain tasks will need to be deleted, some amended in their description and/or frequency, and perhaps some new tasks need to be added addressing a significant failure mode not previously addressed. The effects of these changes, both in terms of when the PM needs to be conducted and the duration of the PM itself, now need to be determined in both the grouping of tasks by trade/frequency/equipment state and the sequencing of the tasks within these groups.
Generate the work instructions
Once the grouping and sequencing of tasks is performed, the existing work instructions will need to be amended to reflect the modifications to tasks, grouping and sequencing. This is also an opportunity to review the quality of your work instructions in order to minimise the risk of errors being introduced during maintenance. A master copy of each instruction may have been created in Microsoft Office Word which will need to be amended, reviewed and approved.
Upload the new PM plans and work instructions to the CMMS and document management system
The new and revised plans will need to be uploaded into your CMMS. Also new and amended approved work instructions may need to be transformed into PDF format and updated to the document management system supporting your CMMS.
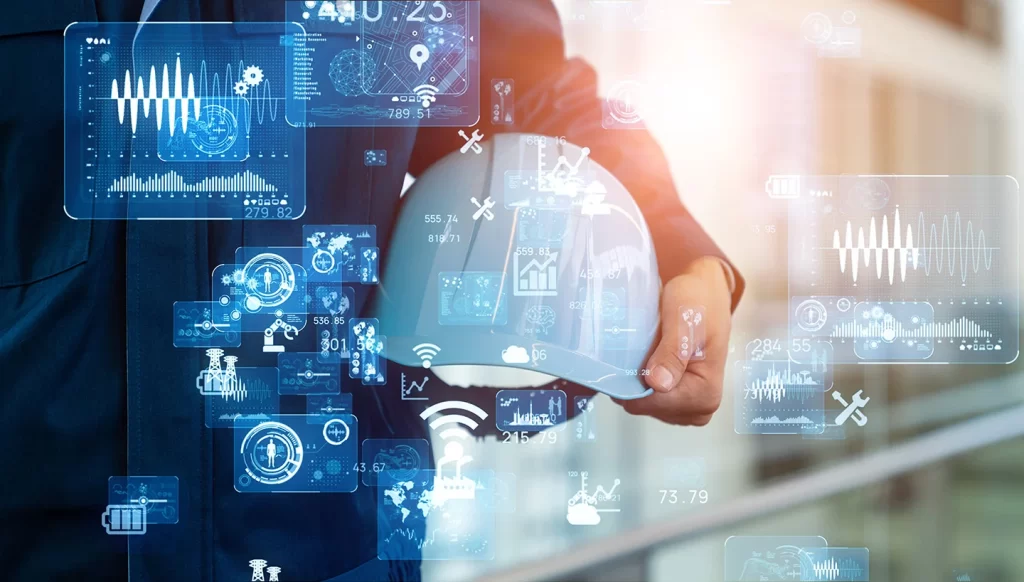
Set the start dates and sequencing for the new PM routines in the CMMS
Someone will need to determine not only the start dates for the revised/new PMs but perhaps also the sequencing. For example, if we have a new yearly routine, do we do that first or sequence it at some time with the suppression of other quarterly routines?
Disable any existing unwanted PMs in the CMMS
The whole point of the exercise is to optimise your maintenance program and eliminate any unnecessary waste. If unwanted existing PMs are not removed at the same time as the new and revised PMs are entered, then these unwanted PMs will continue to be generated in your forward log, causing confusion and potentially wasting valuable resources on already identified unnecessary tasks. This could also potentially cause unnecessary backlogs.
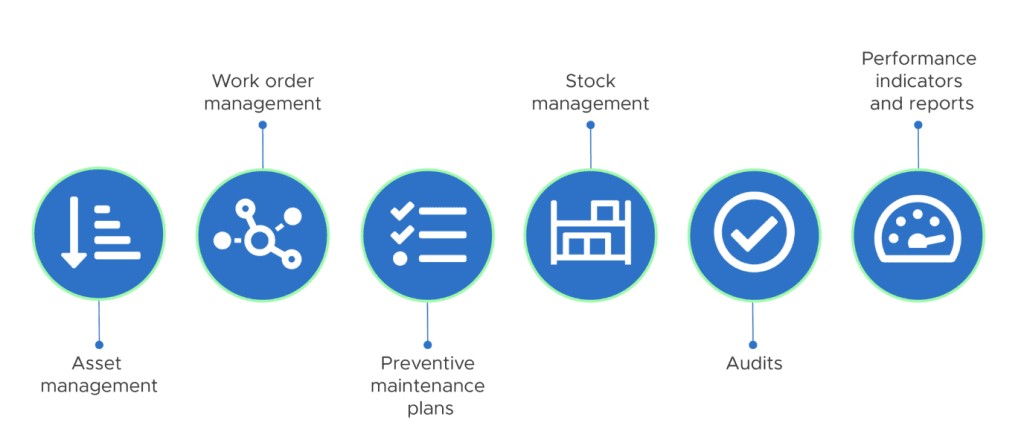
Ensure that any tasks assigned to Operators are included in Operator SOPs and check sheets
Maintainers are not the only ones who do maintenance. The review of your PM program will determine the right work that needs to be performed by operators to ensure reliable equipment performance. A task performed by an operator in one organisation may be performed by a maintainer in another. For example, cleaning a probe on an analyser. Consequently in determining the right work for your optimised maintenance program, any applicable operator tasks added or amended must be reflected in updated operator SOPs and/or check sheets.
Communicate the change
If changes to the PM program have been made, ensure that these changes have been communicated to all those maintainers and operators that are affected by the changes. Effective communication will foster ownership.
Train for change
If changes to the PM program have been made, ensure that these changes have been communicated to all those maintainers and operators that are affected by the changes. Effective communication will foster ownership.
Design modifications
Sometimes the PM program review may reveal that a modification to the existing design may be the best solution to reduce the likelihood and/or consequence of failure of that system. These identified modifications will now need to proceed through your organisations’ engineering management system for consideration. If approved and funded, through the implementation of the modification process, the engineering team should also consider the delivery of an optimised maintenance program. All the points mentioned above will also need to be performed as part of the implementation of the modification to ensure that waste in the PM program is not introduced.
One time changes
In addition to design modifications, sometimes changes to the operation of equipment, eg. operating practices or parameters can help reduce the likelihood and/or consequence of failure of the equipment and/or potentially reduce the PM burden on the system. Consequently any such changes identified during the review need to documented, implemented and sustained as standardised practice in applicable operating procedures.
Unfortunately in many organisations all of the above steps don’t happen and the potential benefits of doing the right work through an optimised maintenance program are not achieved. We are aware of one organisation that decided to conduct a review and optimisation of their existing maintenance program for one of their facilities using a PMO approach. After all this hard work had been done, involving a considerable number of personnel and utilising a considerable amount of time, the results of the review had still not been implemented several years on. Consequently with the same sub-optimal existing maintenance program place, identified waste had not been removed and was continuing to occur. Obviously none of the benefits desired from the maintenance review were being realised…since it hadn’t been implemented. The whole exercise of performing the maintenance review was therefore a waste of time, resources and cost to the business from the lack of implementation. This lack of implementation could also lead to barriers to success being created by those involved in any other future maintenance reviews.
The bottom line is if you are going to review your maintenance program, make sure you treat it like a proper project and follow it through from its conception through to its closeout. What you define as your closeout is up to you but at minimum it should be all the elements of implementation as described in this article.
If you enjoyed this article and want to receive notifications of future articles that we publish, please sign up for our newsletter here.