Ensure you are avoiding premature failure.
Numerous research studies have shown that over 50% of all equipment fails prematurely after maintenance work has been performed on it. In their ground-breaking work that led to the establishment of the technique that we now know as Reliability Centered Maintenance (RCM), Nowlan and Heap1 found, when analysing the failures of hundreds of mechanical, structural and electrical aircraft components, that more than two-thirds of all components demonstrated early-life failure, as illustrated below.
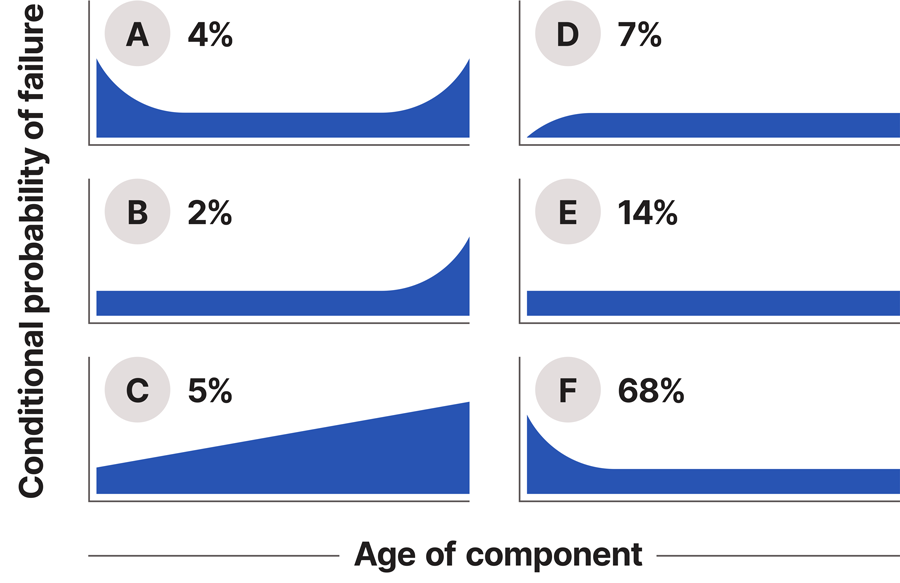
Another study estimated that maintenance errors ranked second to only controlled flight into terrain accidents in causing onboard aircraft fatalities between 1982 and 1991 (despite the application of RCM techniques in the airline industry during this period)2. A study of coal-fired power stations indicated that 56% of forced outages occur less than a week after a planned or maintenance shutdown3. A further study indicated that maintenance activities contributed to at least 80% of all inflight engine shutdowns (IFSDs) in Boeing aircraft. Addressing this issue is one of the greatest improvement opportunities that exists for maintenance organisations today. The costs of poor maintenance quality are huge, but remain, for the most part, hidden, and therefore the opportunity unrealized.
How we can support you
Our approach to addressing premature failure involves:
- Admitting that maintenance error is inevitable and designing systems and processes around this inevitability;
- Using Reliability Centered Maintenance (RCM) and Preventive Maintenance Optimisation (PMO) to ensure that equipment is not being unnecessarily over-maintained (thereby reducing the risk associated with the fact that this work may not be performed correctly); and
- Designing tasks, jobs and workplaces to improve the quality with which maintenance activities are performed.
Our consultants can assist you to improve the quality with which maintenance work is performed, and realise the benefits of improved equipment reliability by:
- Working with you to optimise your preventive maintenance program using RCM or PMO to ensure that equipment is not being over-maintained
- Providing training to tradespeople to make them aware of the factors and situations that may lead them to be more error-prone
- Designing and implementing effective handover procedures (between tradespeople, workgroups and shifts) that reduce the likelihood of errors occurring
- Establishing competence and work allocation frameworks that ensure that only individuals that are qualified to perform a task are assigned to that task
- Improving the quality of maintenance planning and scheduling to ensure that all resources required for a task are available, reducing the likelihood of dangerous short-cuts and workarounds being required to complete tasks
- Improving the quality of task documentation to ensure that high risk activities are identified and highlighted, and appropriate risk reduction steps put in place
- Working with you to design and implement Defect Elimination and Root Cause analysis processes that effectively address human error by understanding and dealing with the organizational factors that contribute to these errors occurring
References
- Nowlan FS and Heap H – Reliability-centered Maintenance. Springfield, Virginia: National Technical Information Service, US Department of Commerce, 1978.
- Smith A – Reliability Centered Maintenance – Boston, McGraw Hill, 1992
- Davis RA – Human Factors in the Global Marketplace – Keynote address, Annual Meeting of the Human Factors and Ergonomics Society, Seattle, 12 October 1993
Related case studies
Let’s evaluate your maintenance quality.
We can support and guide you through the evaluation and improvement of your maintenance processes. To find out more about our capabilities with regards to reliability improvement, feel free to view the case studies above, or contact us for an obligation-free discussion.
Our reliability training courses
Do you need to expand the reliability capabilities of your team? We offer a range of reliability improvement courses which offer a comprehensive overview of reliability best practices. Speak to us to discuss in-house training, or customising any course for your organisation.
-
RCM & PMO for Team MembersOriginal price was: $2,150.00.$1,935.00Current price is: $1,935.00.
-
Reliability Excellence FundamentalsOriginal price was: $4,795.00.$4,315.50Current price is: $4,315.50.
-
Root Cause Analysis for Team MembersOriginal price was: $2,150.00.$1,935.00Current price is: $1,935.00.
-
Introduction to Reliability ImprovementOriginal price was: $1,075.00.$967.50Current price is: $967.50.
Our reliability improvement articles